Introduction
Physical and Chemical Properties of Cockle Shell
Cockle Shell Preparation
Fresh Properties
Workability
Setting Time
Other Properties
Thermal Conductivities
Porosity and water permeability
Application of Cockle Shell in Other Research
Conclusion
Introduction
Cheap, wider availability, great load-bearing capacity, and a wide variety of construction engineering applications are the primary reasons for what causes concrete is the most used construction material. Traditional concrete is usually weak in tension yet vigorous compression activity [1]. Consequently, in tandem, cement usage with concrete production is increasing. For example, in 2018, Portland cement was used for about 4 billion tons annually [2] and is expected to significantly grow in production in China, India, and certain areas of the Middle East and North Africa [3, 4]. The production of Portland concrete has a significant environmental impact because of CO2 emissions, representing 5 to 8% of carbon dioxide (CO2) emissions per year [5, 6]. Portland cement clinkers [7] are primarily responsible for CO2 emissions. The CO2 emissions created by the decomposition of raw materials during clinker combustion [8] are termed process-related CO2 emissions from concrete manufacturing, primarily caused by the breakdown of CaCO3 when heated [8, 9]. As indicated in Figure 1, the overall emissions from the industrial sector (excluding power sectors) constitute approximately 20% of global carbon emissions, except for direct emissions related to energy use [10]. In addition, a considerable quantity of (about 20%) emissions is produced by industrial manufacturing activities, including cement, chemical manufacture, lime production, and so on, as well as indirect energy usage emissions [11].
Apart from clay, calcined limestone is a major component of cement. It is a sedimentary rock mostly composed of calcium carbonate (CaCO3). Because limestone is a non-renewable material, its resources are limited, and its stocks either do not regenerate after mining [12] or take a long time to replace [13]. Mining continues to jeopardise resource depletion [14] and environmental degradation [14, 15]. Stone extraction from the hill, which necessitates the removal of trees and plants before they can be harvested, depletes green forests, and adds to global warming concerns. Deforestation has disastrous consequences, including soil erosion, greenhouse effect, biodiversity loss, increased floods, and droughts. The loss of flora and habitat has ramifications for the entire ecological system [16] and hastens the extinction of living organisms. Also, cement production pollutes the environment, including the air [17], water, and land, and contributes to noise pollution [12]. As a result of the cement industry’s negative impact, environmental activists and communities will benefit from using local trash as an alternative resource to reduce reliance on non-renewable products. This strategy would also keep the area from becoming a dumping ground [18].
The increased worldwide use of concrete, environmental concerns, the need for optimal material use, and the positive effect of SCMs on concrete characteristics are driving the widespread use of supplementary cementitious materials (SCMs) in the concrete industry [19]. However, the amount of waste produced worldwide is increasing, posing a threat to the environment and human health. One of the most severe environmental concerns is industrial trash dumping. Several tonnes of industrial by-products are dumped in landfills, polluting groundwater, and destroying natural soil, including cockle shells. In addition, cockles play a vital role in the ecosystem services that many other services rely on [20]. It has a high economic value and is widely exploited throughout its range [21]. In 2019, it has been reported Malaysia exported 538 tonnes of clams, cockles, and ark shells however the amount is increasing in 2020 to 947 metric tonnes [22]. According to the Wild Fact Sheet, the physical characteristics of the cockle shell are approximately 3 to 4 cm in size [23]. The double-shell has a spherical shape and is quite heavy. Most cockle shells are dumped in open sites or sites where only a small percentage is recycled for other purposes, such as fertilizer and handicrafts.
In contrast, others are disposed of in open fields and sites, giving rise to unappealing odors [24] due to the meat’s degradation in the shells or the microbial breakdown of salts into gases like H2S NH2 and others. According to the facts, a cockle shell is an innocuous substance with a high concentration of the CaCO3 chemical. Calcite, aragonite, and vaterite are polymorphs of calcium carbonate (CaCO3), one of nature’s most common minerals [25, 26]. Aragonite has a robust mechanical strength and a moderate biodegradation rate, enabling long-term performance [27].
Physical and Chemical Properties of Cockle Shell
The physical features of a cockle shell concrete are determined using Scanning Electron Microscopy (SEM), as shown in Figure 2. Figure 2[28] shows the hydrated cement matrix morphologies produced in mixed cement mixtures, including seashell powder. Also, according to Figure 2, some ettringites, especially calcium carboaluminate, occur near or on the seashell powder location, which could partially explain why seashell powder enriches hydrated cement matrix, or instead form composite matrixes, compared with 100% OPC and promotes precipitation of hydration products, ettringites. This is one of the benefits of seashell powder into mixed cement; it helps build a new hydrated cement matrix with greater integrity and cohesion.
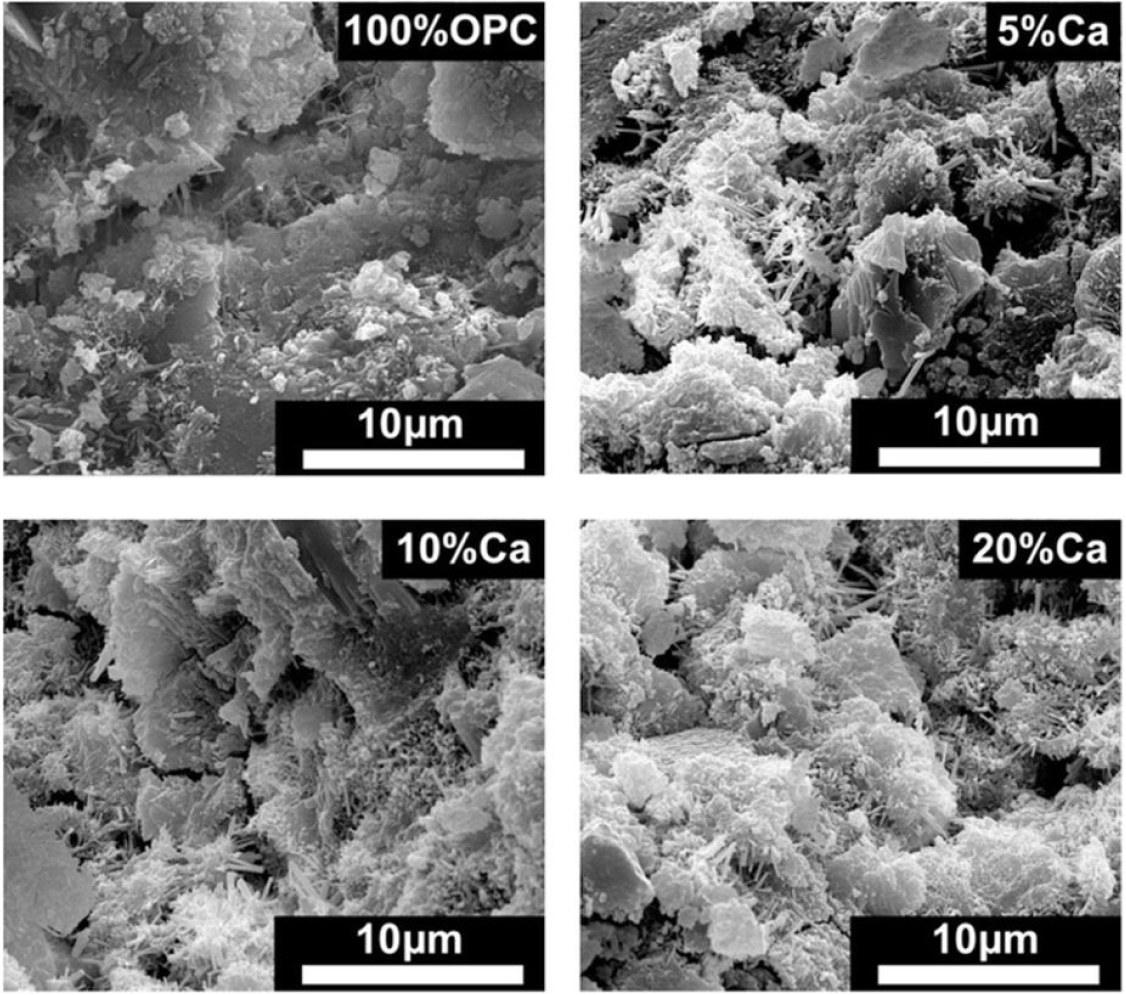
Figure 2.
Microstructure of hydrated cement matrix produced in the presence of seashell powder in a mixed cement mixture [28].
Table 1 and Table 2 show the cockle shell’s chemical properties for unburned and burned cockle shells, respectively. CaO is generated after the decomposition of CaCO3 has been performed [26]. As seen in Table 2, the CaO content is 99% that the cockle shell undergoes a calcination phase of less than 1000°C to form cement-like ash. However, as seen in Table 2, CaO content is 51.56% when burned at 500°C, while it was 51.91% when burned at 600°C and has the same volume of CaO as unburned cockle shell as seen in Table 1. This could lead to a firm hypothesis that the mechanism of calcination of the cockle shell at higher temperatures would decompose CaCO3 to higher CaO levels. Additionally, the burning of seashells reduces them to microscopic particles by destroying the chemical bonds between the molecules [29]. Additionally, the seashell burning method eliminates the need to mill the seashells since the burning process between 700°C to 900°C produces a more refined product and converts the compound from CaCO3 to CaO [30, 31, 32, 33].
Table 1.
Chemical properties cockle shell powder in percentage (%)
Reference | SiO2 | Al2O3 | Fe2O3 | CaO | MgO | Na2O | K2O | SO3 | SO4 | CL | LOI |
[32] | 0.98 | 0.17 | 0.06 | 54.24 | 0.02 | 0.37 | 0.03 | 0.13 | 0.07 | 0.01 | - |
[33] | 3.65 | 1.15 | 0.20 | 52.34 | 0.42 | 0.35 | 0.13 | 0.47 | - | - | 41.252 |
Table 2.
Chemical properties cockle shell ash in percentage (%)
Reference | SiO2 | Al2O3 | Fe2O3 | CaO | MgO | Na2O | K2O | SO3 | SO4 | CL | LOI |
[34] | 0.38 | 0.65 | 0.05 | 51.91 | - | - | - | - | - | - | - |
[35] | 1.60 | 0.92 | - | 51.56 | 1.43 | 0.08 | 0.06 | - | - | - | 41.84 |
[36] | 0.07 | 0.03 | 0.05 | 99.0 | - | 0.49 | 0.06 | 0.14 | - | - | 0.20 |
Cockle Shell Preparation
Raw cockle shell goes through a specific process before replacing cement in concrete. However, every study has different ways to prepare the material. Table 3 shows the preparation process of the cockle shell before it was used for cement replacement in concrete.
Table 3.
Cockle shell processing method
References | Replacement type | Cockle Shell Process Method |
[37] | Cement powder | The shells were cleaned with water to remove soil and boiled for 2 hours to remove the traces of cockle meat and odors until the air was dry for 12 hours. The calcination process lasted for 2 hours at a temperature of 500°C. Before pulverizing, the burnt cockle shell was then smashed into 1⁄2 1 mm range powder. |
[32] | Cement powder | The seashells were cleaned, dried, and ground by a harsh grinding machine. The shell passed through a sieve of 4.47 mm and then wet-milled for 3 to 4 hours to further pulverize the shell until the particle sizes were smaller than the sieve of 0.075 mm. The shell powder was oven-dried at a temperature of 110 ± 5°C for 24 hours. |
[33] | Cement Powder | The shells were washed twice and dried in the oven at a temperature of 70 ± 5°C for 48 h. The shells were then crushed using a steel drum revolving grinder and further pulverized by a grinding mile until the shell particles reached a minimum surface area of 3800 cm2/g. |
[38] | Cement Powder | The shells were washed with water to remove the soil and washed in the oven at 100°C for 2 hours. Clean shells were mainly crushed into small parts using a JFSD 100 crusher. The crushed shells were subjected to dry balm milling at 200 rpm for 24 hours to yield fine particle-sized powder (0.6 μm). |
[36] | Cement Ash | The shells were cleaned to extract the soil and dried in the oven at a temperature of 105±5°C for 24 hours. The shells were ground in powder to move 5 mm of the sieve with a cone crusher before being burned at 1000°C for 1 hour in a gas furnace at a heating rate of 10°C/min. After that, the cockle ash was left to cool at room temperature for at least 24 hours before being used. |
[34] | Cement ash | The ash shells were formed by washing, drying, burning the shells in the brick furnace for 3 days at approximately 600°C, grinding, grounding, and sifting the shells using the #200 sieve. |
[35] | Cement ash | The shells were washed, dried, burned in a brick furnace, crushed into small pieces using a Los Angeles unit, ground with a blender, and sieved with a #200 sieve to process shell powder. The shells were burning at a high temperature of 500°C for 3 days. |
Fresh Properties
Workability
As partial coarse aggregate replacement increases, the percentage of cockle shells supplied lowers concrete workability. However, as the amount of cockle shell used increases, the mixture’s rough-textured component causes it to become harder, making it more difficult to blend and resulting in a lower slump value. This might be related to the cockle shell being rougher than natural aggregate. The more irregular surface causes greater friction, lowering the fluidity of the liquid containing a higher amount of cockle shell [39]. However, when cockle shell ash is substituted for cement, it typically has the same impact trend on a workability slump. The slump value decreases proportionately to the rate of replacement of cockle shell ash [36]. The list of data is provided in Table 4 below.
Table 4.
Workability of cockle shell concrete
Reference | Type replacement | Replacement (%) | Slump (mm) |
[36] | Cement ash |
0 5 10 15 25 50 |
90 60 30 10 5 0 |
[39] | Coarse aggregate |
0 5 10 15 20 25 30 |
55 46 45 25 23 10 8 |
Setting Time
The original set time is the allowable period for the remaining freshly poured concrete to be worked. For OPC, a minimum of 45 min is defined. On the other hand, the final environment should not be too long to prevent needless delays in the production of concrete power. The findings reveal that the initial setting time of the blended cement varies from 1 h 30 min for 0% cockle shell ash sample to 3 h 20 min for 50% cockle shell ash sample, while the final setting times vary from 3 h 30 min to 5 h 7 min for 0-50% cockle shell ash samples. It is noted that the inclusion of cockle shell ash has slowed cement setting times. By applying cockle shell ash to the concrete, both the original and final setting times improved because cockle shell ash was used [36]. The same is true of Lertwattanaruk [32], which suggested that when the ratio of ground cockle shell substitution in Portland cement improved, there was an increase in the initial time of formation. Olivia [34], however, has obtained contrary conclusions. For example, it has been documented that the final time for OPC cockle concrete is shorter than the OPC concrete. On the other hand, Muthusamy et al. [40] discovered that increasing the percentage of cockle shell powder in the paste from 20% to 40% increases the amount of CaCO3, causing the paste to become rigid in a shorter amount of time during the setting process. The overall data on setting time research is tabulated in Table 5.
Table 5.
Setting times of cockle shell cement paste
Reference | Cement Replacement (%) | Setting Times (mins) | |
Initial | Final | ||
[34] |
0 4 |
80 80 |
138 106 |
[36] |
0 5 10 15 25 50 |
90 150 180 180 190 200 |
210 250 270 290 310 340 |
[33] |
0 4 5 6 7 8 9 10 15 20 30 |
60 77 77 77 77 85 105 105 105 120 120 |
90 93 90 90 93 93 135 120 135 135 135 |
[39] |
0 10 20 30 40 |
120 135 120 105 120 |
210 225 195 195 180 |
Other Properties
Thermal Conductivities
According to Lertwattanaruk [32], mortars with cockle shells exhibited lower heat conductivity than control mortars (refer to Figure 3). Increased percentage replacement of ground cockle shells diminishes mortar thermal conductivity due to the lower specific gravity of these ground cockle shells compared to cement. With the introduction of these field cockle shells, mortar density decreased, porosity rose, and thermal conductivity decreased. On the other hand, mortars have the lowest heat conductivity because the shell has the largest particle size and the smallest essential surface area, allowing capillary pores to grow. This situation leads to a less compact interior structure and lowers heat conductivity. Thermal insulation has improved with higher thermal conductivity materials. Al-Zubaidi [38] makes the same findings and assumptions as Lertwattanaruk [32]. The rise in cockle powder in the specimen, followed by a drop in cement content, increased the volume of the specimen, which resulted in a decrease in the density specimen. The thermal conductivity of the cockle shell powder-free specimen was 0.004 W/m. K. This value was observed to decrease with the addition of shell powder to the specimen, reaching a thermal conductivity of 0.0023 W/m at a cement ratio of 50% powder. This indicates that the cockle shell material has lower thermal conductivity than the mortar, thus improving the specimen’s thermal insulation is attributable to the powder’s inherent low cockle shell conductivity.
Porosity and water permeability
Porosity is a vacuum that exists in a constant or discontinuous form on the interior and external surface of the concrete and affects the strength of the concrete. At the same time, permeability is a means of evaluating concrete resistance to adverse events, and more solid concrete should be waterproof [36]. By using the volumetric method, vacuum quality has been measured. The empty content may grow as the waste percentage is also raised, according to Khankhaje [41]. This may be owing to the cockle shell’s angular existence, which reduced the compactness of any cockle shell mix and thus perturbed the cockle shell’s granular composition. This is due to the high-water absorption of particles that absorbed more water during the mixing process, thereby trapping the air on the mixture’s surface, thus increasing the void content of the mix. It looked like a vacuum consistency of perpetual concrete mixes was the impact of waste substances on water permeability. Therefore, it was anticipated that the water permeability of perpetual concrete mixtures would similarly rise to a high void value as a regular gross aggregate by increasing the proportion of waste material replacement. Hazurina [36] has determined that, given the average porosity findings, concrete porosity would be reduced by increasing the cockle shell ash replacement ratio except for 25% and 50% (Refer Table 6). The amount of cockle shell ash as a substitute for cement was also reported not to be over 15%.
Figure 4 shows the effect on the permeability of the concrete mixes of the cockle shell. The labels, ‘1’ and ‘2’, referred to the size of the coarse aggregates used, big (6.30-9.50 mm) and small (4.75-6.30 mm), respectively. The impact of the waste materials on the water permeability was similar to the empty substance of the porous concrete mixes. It was thus anticipated that the water permeability of previous concrete mixes would also improve due to the scaling of void quality by increasing the proportion of wastes to be replaced for a natural ground aggregate [41]. In the previous concrete blends, the water permeability coefficient ranged from 3.5 to 15.2 mm/s.
Table 6.
Water permeability of concrete mixtures [36]
Application of Cockle Shell in Other Research
Cockle shell has been noticed to be used as construction material. However, the usages of cockle shells in other research applications are also found. Cockle shell has been widely used for many industrial purposes. For instance, it is applied as a biomaterial for tissues engineering. Cockle shell has been investigated as artificial bones substitute material or best known as bone grafting material [42, 43]. This material replaces unhealthy tissues in an individual [44]. The reason is that orthopedic implant in the USA has a high demand. Previously, the implantation was made from a coral exoskeleton. However, it creates environmental issues because the coral exoskeleton is endangered. Besides that, cockle shell has also been derived as Nanomedicine for drug delivery system in the body via blood capillaries [27]. It also reported that cockle shells could be used for wastewater treatment. The cockle shells are converted into calcium oxide (CaO) for the treatment, which acts as a catalyst for eliminating methylene blue through an advanced oxidation process [33]. Historically, photocatalysts such as titanium oxide (TiO2) and zinc oxide (ZnO) have been widely used in wastewater treatment; however, due to the high cost and scarcity of titanium oxide on the earth [45], the researcher desired to explore the efficacy and efficiency of using CaO derived from cockle shell as a new catalyst.
Conclusion
Because of its chemical similarity to limestone, calcium carbonate (CaCO3), cockle shell is an alternative cementing material that is ideally suited to our construction sector with technical, economic, and environmental benefits. As a result, concerned entities should be made aware of the situation and encourage the manufacturing and usage of certain cement types for acceptable purposes. In addition, because cockle shells are abundant with the required chemical composition, it is possible to replace limestone in cement production. According to this review paper, the finding shows that,
1.The workability of fresh concrete decreases as the percentage of cockle shells as cement and coarse aggregate replacement increases.
2.Setting the time of cockle shell as cement replacement from 0% up to 50% fulfills the ASTM1157-08a requirement.
3.Increase in thermal insulation improved with increased thermal conductivity material; however, according to the literature review, cockle shell material has lower thermal conductivity.
4.The suitable amount of cockle shell ash as cement replacement for porosity and water permeability is not over 15%.
In a nutshell, future experimental work related to cockle shells as construction material replacement should be emphasized, especially for durability aspects, such as water absorption and density of concrete, acid attack, etc.