Introduction
Need of the Research
Aim
Objective
Research Questions
Scope and Limitations
Important Definitions
Project Proponents (PPs)
Products
Dis-assembly
Circular Economy (CE)
D-Tools
Industry 4.0
De Construction Plan
Literature Review
Industry 3.0 and Industry 4.0
Urban Planning – RP, DP & TP
Background
Study Area – Pune City region, Industrial Revolution’s impact
Materials and Methods
What is done in the research
How the research tests/experiments/surveys/case studies are done-
Tests and Results
Regional Planning
Urban Planning and Urban Design
Architecture and Interior Design
Preferred Circular Economic Tools for Designed Disassembly
Covid 19, Industry 4.0 and Society 5.0
Conclusions
Introduction
In 2015, the United Nations (UN) adopted the 2030 agenda for Sustainable Development, which set out 17 Sustainable Development Goals (SDGs), 169 targets and 231 unique indicators as a significant initiative towards socio-economic development [2]. Focus area for this paper is the 12th SDG which is Responsible Consumption and Production (Figure 1). The paper tries to look at management of construction demolition waste in the context of Circular Economy and Industry 4.0. As the various industrial revolutions (IR)s took place from early 18th century till date, it has degraded the environment, increased global warming and impacted climate change. As quoted by D. Gasper, incorporation of SDG 12 process was initiated long back, “This was the culmination of discourses on sustainable consumption and production (which) have featured in UN discussions on the environment and sustainable development since 1972” [3]. Since then, the global north and global south are debating on implementation of SDGs to understand their roles and responsibilities, particularly SDG 12. The 6th Assessment Report of the IPCC’s Working Group has issued a “code red” warning: climate change is “widespread, rapid and intensifying” and the world looks set to exceed the Paris target of limiting global warming to 1.5°C above pre-industrial levels as early as 2035 [4]. SDG 12 which is Responsible consumption and production: ensures sustainable consumption and production patterns [2] and has got 11 supported targets and 13 measured indicators to monitor its performance. Concept of Circular Economy (CE) as framed by the Ellen MacArthur Foundation, “an industrial economy that is restorative or regenerative by intention and design” [5] could be the way forward. Design of the product and use of resources in the product’s multiple life cycles are the biggest design challenge for the CE today. As a crucial economic sector, the construction industry is responsible for up to 33% of all emissions, around 40% of all material consumption, and 40% of all waste [6]. In the built environment, Construction & Demolition (C&D) waste is the solid waste generated in the construction, maintenance, and demolishing process of buildings or structures [7]. This paper tries to understand impacts of each IR i.e., from Pre to post Industry 1.0, 2.0,3.0, 4.0, its impacts on management of Construction demolition wastes (CDW) and its linkages to tools that are used for demolition purposes and management of waste in the environment. Management of waste in megacities is a challenge that needs to be addressed at various scales as “the construction industry generates a huge amount of C&D waste which ends up in landfills disturbing the environment and ecological balance” [8]. CDW is generally dumped in ecologically sensitive areas like hills, foot hills water bodies, streams, canals, rivers, etc, which has major impacts leading to disasters like flash floods and loss of ecology.
Need of the Research
The last 150 years of industrial evolutions have been dominated by one-way or linear model of production and consumption in which goods are manufactured from raw materials, sold, used, and then discarded as waste [9] which is known as a linear economy. Circular Economy is a concept that stems from the need to address environmental degradation, social unrest and inequalities, institutional instability, resource scarcity, and economic challenges caused by the linear nature-society-nature systems that the large portion of society operates on [10]. Industry 4.0 is also about management and use of data resources for environmental protection as “an integration of RFID1) tags and digital models of building components through BIM2) gives designers additional capability to track, identify, locate and select appropriate objects currently in use, each with a unique ID3) allotted, to incorporate into BIM models for new buildings” [6] and this helps in achieving responsible production and consumption goal SDG12. In the current literature, the conventional linear economy model of “take, make, and dispose” prevails, leaving many questions unanswered [11]. (CE) strategies hold the key to a resource efficient, low-carbon, and inclusive future [12].
Indian construction industry follows linear economic pattern for consumption of natural and manmade resources that are used for development of built environment. The resources need to be used, conserved and reused in a sensible way because all them are scarce and their consumption means direct or indirect consumption of energy, emission of Co2 and greenhouse gasses. Raw materials scarcity, rising raw materials extraction cost, and biodiversity loss are apparent globally. Recycling of materials for a (CE) is cited as one solution to those problems [13]. This will require radical rethinking of how resources are used and moved through different cycles, and of the roles of different actors involved in the value chain [11]. Global north and China from Global south are working on the concepts of (CE) and looking at the waste as a resource. Various governments, multinational companies, and the finance industry can take practical approaches in their (CE) strategies to include and support small- and medium-sized suppliers located in the developing world [11]. Legal framework with the aim of transforming our common inhabitation of the planet from a system of exploitation to a system of stewardship of the Earth System through a process of self-organization to manage its use [12], can be the way forward. This work of research tries to look at resources, construction demolition activities, advanced construction demolition tools and its current usage in the context of Industry 4.0
Aim
To understand the impacts of D-tools in deconstruction activities in the context of pre- and post-industrial revolution eras from (CE) perspective.
Objective
1.To understand the relationship between IRs and their impacts on evolution of tools, expression of built forms and urban spaces.
2.To understand the impact of Industry 1.0, which started from 1784 - mechanization - the invention and implementation of the steam engine introduced repeatable production and the era of industrialization; [14] on CDW.
3.To understand the impact of Industry 2.0, which started from 1870 - electrification - electricity displaced steam engines, and production lines could produce goods in large series; [14] on CDW.
4.To understand the impact of Industry 3.0, which started from 1969 - digitization - the invention of the microprocessor and increasingly efficient computers and data processing systems have enabled machine control using the software [14] on CDW
5.To understand the impact of Industry 4.0 - integration of systems and the creation of networks based on communication and development of artificial intelligence (AI). [14] on CDW.
Research Questions
Research questions are based on IR, CE, CDW, tools used for CDWM. Few sample questions are enlisted as an example - Did each industrial revolution pose a great challenge to humanity? Were the impacts of each industrial revolution positive or negative on the environment and society? Was society prepared to absorb these IRs and their impacts? Why, how and where was the built environment affected due to each industrial revolution? Did each industrial revolution increase the CDW? Did the project proponents (PP)s utilize technology to reduce the CDW and its impact on environment? As the various IRs progressed, did new technology, tools, test, materials, products, systems, and processes evolve to help solve the issues of environmental degradation? Or did these issues increase? Did each IR affect the design of the products, it’s life cycle, consumption of resources in product manufacturing etc.? This paper tries to link IRs, CE, and CDW management to avoid environmental degradation.
Scope and Limitations
Pre-IR and Post-IRs i.e., one, two, three and four IR (I 1.0, I 2.0, I 3.0 and I 4.0) brought about new innovations in various economic sectors. Construction technologies transformed due to innovations in technology, materials, techniques of construction, adoption of new skills by its users. All these IRs were accompanied with various challenges to society related to public health, socio economic, and environmental challenges, for example - floods, earthquakes, pandemics like plague, cholera, to Covid 19, etc. Each IR brought about new materials, skills and technologies which had positive and negative economic, socio-cultural impacts. At the same time due to each IR, expression of architecture and quality of life in public spaces also transformed. The question is did we use each IR to protect the environment by using technological advancement? Did we use technology to its fullest extent? This paper defines its scope for understanding the direct and indirect impacts of each IR on built environment and urban spaces. To pin point, it further it tries to probe into issues related to CDW in the Indian context and with particular focus in Maharashtra state4) which has experienced all these transformations in pre- and post-IRs. It limits its scope to understanding the use of construction demolition tools and Industry 4.0 technology from CE perspective. It looks at CE from broader perspective and does not enter in to micro level issues of architectural projects and its demolitions. Architecture scale scope can be dealt as separate research work. In this research management of CDW at macro and meso levels are looked as an opportunity for transformation of linear economy to CE.
Important Definitions
Project Proponents (PPs)
Are a team of stake holders, owners, architects, structural designers, MEP consultants, contractors, and computer software data scientists working together in Industry 4.0 with goals and objectives aligned towards a (CE).
Products
All types of construction, deconstruction activities in rural and urban areas, including public infrastructure works like road, bridges, culverts etc and buildings as well.
Dis-assembly
Demolition, de construction and dis-assembly of the products to minimize the impact on environment by reducing waste and boosts (CE) at the same time by helping to repurpose the waste.
Circular Economy (CE)
The (CE) is a systems solution framework that tackles global challenges like climate change, biodiversity loss, waste, and pollution [15] Uses the 3Rs –Reduce, Reuse and Recycle, in simple words it means, reuse all the resources during design, execution, and after life of the products for minimizing it’s impact on the environment.
D-Tools5)
PP selects/recommends use of specific advanced deconstruction tools called D-Tools for product demolition purpose, to try to gain carbon credit points through (CE). These credit points are measurable, linked to artificial intelligence and would be deposited on cloud, which would help fetch rewards.
Industry 4.0
It is the Industrial Revolution that provides real time data, interconnectivity, automation & machine learning that helps interface between machines & humans, in simple words it means ‘the one who will control the data will rule the world’.
De Construction Plan
A Green plan created by PP with recommendation of D tools for the product deconstruction, demolition and disassembly which will help to receive measurable credits with the help of Industry 4.0 and create green jobs6) in construction sector and boost (CE).
Literature Review
The Industrial Revolutions, Deconstruction tools, (CE), construction demolition waste management, and urban planning were keywords used for literature search. Global warming, climate change, global north, global south, and SDG was a larger canvas under which CE, I 4.0 and CDW management were reviewed.
The review is divided into four components and each component is further probed as shown in the Figure 2. The objective of the review was to understand each industrial revolution and its relation to CDW management. But during this exploration, lot of opportunities, issues and concerns related to CE & I 4.0 technology came in the light. Relations of IRs, D-tools, CE scales (macro, meso & micro) helped to relook at the current practices of CDW management.
In the Pre-Industrial revolution period, architecture and cities evolved due to cultural beliefs of castes, caste-based roles for artists, craftsmen, and tradesmen. Bhakti sampradaya7), contribution of Saints like 8)Jayneshwar Maharaj and 9)Tukaram Maharaj and their value education was the driving force in generation of a socio culturally close-knit society in Maharashtra. Various rulers and religious saints influenced the architecture and settlements grew. Arts and crafts of construction and de construction tools also got transformed as we progressed through each industrial revolution. During this process, it questions the product and product proponent’s role during and after life cycle of the product. The research challenge was to understand influence of industrial evolutions, and its linkages to science, technology, architecture, settlements and their impact on CDW management.
The term Industrial Revolution ‘IR’ was first popularised by the English economic historian Arnold Toynbee (1852–1883) to describe Britain’s economic development from 1760 to 1840. IR initially meant ‘complete change in the relationship between employers and employees brought about by mechanical inventions in the late 18th and early 19th century’ [14] I 1.0 started with invention of steam engine in United Kingdom (Figure 3). This IR transferred the rural industries into towns and craftsmen became wage laborers. “The IR was the transition from human and animal labour technology into machinery, new chemical manufacturing and iron production processes, improved efficiency of water power, the increasing use of steam power, and the development of machine tools” [16] New inventions took place and they helped to generate economic activities; settlements started growing people started living close to economic/ production hubs. These economic activities subsequently led to wellbeing, economic growth and impacted the environment. I 1.0,2.0,3.0 each of these revolutions increased the consumption of resources which was take, make and throw pattern i.e linear economic models. Now I 4.0 offers us the opportunity to convert the linear economy to a circular economic model. Each IR brought its own unique opportunities and challenges along with it. They were related to biosphere10), Technosphere11), and public health which started posing challenges to the people and settlements.
Industry 1.0 and Industry 2.0 - The First IR began in England in about 1750–1760 that lasted to sometime between 1820 and 1840. It is one of the most distinguished turning points in human history. During this period human and animal labour technology transformed into machinery, such as the steam engine, the spinning jenny, coke smelting, puddling and rolling processes for making iron, etc [16]. During the period of Industry 1.0 and 2.0, India was a British colony. The British utilized cheap Indian manpower and exported raw materials and imported finished goods to India. For an efficient transportation system, Britishers developed the rail routes within India and Sea routes and ports were used for connection to UK. Due to this, Indian Ports like Calcutta and Mumbai started growing in to cities and industrial activities also started increasing. Amongst them, “Mumbai emerged as the largest commercial and industrial centre of India on the basis of port facilities and also due to its large‐scale industry such as cotton textile mills, which started operation around 1850” [17]. After sudden surge of textile mills in Mumbai, the city saw a huge influx of population migrating to Mumbai. Due to this, issues related to health and sanitation started cropping up in Mumbai. The outbreak of pandemics like plague and cholera were also experienced by the city. Mumbai being an island city, shortage of land and increased demand for housing forced citizens and developers to think about alternative materials and technologies for execution of high-rise buildings. Traditional Indian arts, crafts, and construction workers’ skills were not enough to address the issues of housing and its shortage. Due to this PP adopted the use of cast iron and mild steel. This was a major shift where Indian construction workers shifted away from stone, bricks, and timber and started adopting new materials, which can be seen in the Figure 4. Introduction of the cement as construction material had a major impact and it boosted consumption based linear economic model in the construction industry. Faster and more, you produce more is the profit and producer need not bother about its short term or long-term impact on the environment. In the Preindustrial era materials like stone, lime mortar, wood, mud mortar and mud bricks were used and after the life cycle of the product, disassembly and 3 Rs of the product were possible and construction sector was circular economic. In India production of cement started from 1914 at a very low pace and in 1956 The State Trading Corporation (STC) was established for the acquisition and distribution of cement. The main objective was to ensure that both the indigenously manufactured and the imported cement is sold at the same price [18]. This control of the government lasted up to 1977 and after 1977 due to liberalization policy cement started becoming available in the free market. After this stage PP never questioned the linear economic use of cement in the production of RCC12) structures for low, medium or high-rise buildings. Rampant use of RCC was a blind copy of western use of materials and systems of construction. The PP ignored their own circular economic pre industrial product’s design and materials that created major impacts on environment, due to which we are now struggling with the issues of CDW. I 4.0 allows us to relook at this as an opportunity and link it to green economy13) to transform these CDW in to resources.
Industry 3.0 and Industry 4.0
IT & ITES industry got a major boost by the end of millennium change problem Y2K and the Euro currency change problem at global level. The jobs had to be outsourced, which provided an opportunity to the Indian software companies. Many of these companies secured their businesses by not only fixing the Y2K bug but also by providing subsequent improvements in the software, at no extra cost to the customers [19] During this period computer sciences and information technology parks evolved and the service industry needed large workplaces as people started working in densely populated multistoried work places where IT & ITES14) workers worked for outsourced projects. This helped suburban areas to transform into information technology parks through various central and state government policies. Suburbs around Pune city - Hinjawadi, Talawade, Kharadi and Hadapsar saw growth in IT and ITES development in I 3.0 and it created new job opportunities. It helped to create job opportunities in secondary and tertiary economic sectors as well. If I 3.0, I 4.0, Urban Development, environmental protection and creation of green economy are considered as future development trends, then “the subject of green jobs and the fourth IR (Industry 4.0) are the most relevant issues in current modern economy. At the same time, this topic is surprisingly rarely addressed, however it is easy to imagine the creation of new jobs resulting from both development and research conducted in the field of environmental protection” [14] In this context (Refer Table 1), CDW management and its issues need to be addressed using I 4.0 and data management systems. Government of India’s initiative for data management for startups can be seen in the National data governance draft frame work policy which states “to enable and catalyze vibrant AI15) and Data led research and Start-up ecosystem, by creating a large repository of India datasets. This will be achieved by establishing guidelines, rules and standards to build and access to anonymised non personal data to ensure the growth of Indian datasets. This will be the catalyst for Artificial Intelligence and analytics ecosystem, which in turn would be kinetic enablers of India’s digital economy” [20]. The intelligent use of CDW management with the help of I 4.0 and (CE) principles could be the future for green jobs (Refer Table 2). The COVID-19 pandemic may steer the world into the next IR creating Society 5.0 where the amount of information may be impossible for processing by Industry 4.0 technologies [21]. The report ‘Shaping the Future of Work in India’s Tech Industry’ states that “Over 80 percent of the IT companies and GCCs (Global Capability Centers) are most likely to adopt a hybrid work model as compared to the rest of the industry segments. Given a choice, around 70 percent of employees in digital fields would prefer a combination of remote and on-site work models, while 25 percent would opt for completely remote work.” [22] In the given situation what would happen to the existing IT and ITES building blocks and infrastructure that have remained partially closed since the last two years? How do we manage the CDW? Along with Industry 4.0, CDW regional planning infrastructure development can provide a circular economic solution. Central Government of India along with Indian rail ways and Indian Ports has developed freight corridors [23] and Sagar mala projects [24] which respectively can help CDW management (Refer Table 5). Sagar Mala Project helps to connect the sea ports and rail links of proposed and partially executed dedicated freight corridors of 3347 km length, which increases regional connectivity in India. On the west side, from JNPT port to Dadri in Uttar Pradesh 1500 km length and on the Eastern side, 1800km from Dankuni (West Bangla) to Ludhiana (Punjab) [24].
Table 1.
Circular Economy, D Tools & De Construction works
D-Tools | |||
![]() | Manual Tools - Recommended for use in CE, I 4.0 and these can be used for product’s disassembly. Gives good retrieval of resources after product’s life cycle. | ||
![]() | Breakers - Mechanical, Hyadraulic, Electrcial, Explosive - all these types of powers are used for deconstrcution works. This is a linear economic tool focused on retrival of steel. The current use of these tools is not in line with CE & I 4.0 and they are not recommended for deconstrcution works, very poor recovery of resources, focuses on recovery of metal. | ||
![]() | Diamond saw / wires saws- These tools along with I 4.0 and CE principles help design deconstruction. Further due diligence of cost and environmental impact would help to establish them as CE tools. Building elements can be cut in modular sizes and repurposed at macro- CE scale. Can create CE & Green jobs. | ||
![]() | Skera This is a Remote cutting tool, produces fine cutting, does not produce debris, while cutting can be operated remotely, good for accessing most difficult site conditions. These kind of de constuction tools could be the future of CE and it can be integrated with I 4.0. PP needs to design the deconstruction plan. Retrieval rate of de constructed component is better. | ||
![]() | Daqri Helmets - The Intellitrack system uses 360-degree navigation cameras to analyze environments, which in practice means you get something close to X-ray vision on the job site. Intel’s contribution takes the form of an M7 chip and a RealSense camera. The augmented reality has its most useful real-life applications and with its, convenience, safety, and it is smart in use to the everyday workplace [50]. These kind of advanced tools and devices will help to integrate CE & I 4.0. Due to some unavoidable reasons, the company is shut now. More probe is needed in this direction. |
Regional resource imbalances can be an opportunity to upcycle the waste at a regional scale. “Tvasta” developed a ‘Made in India’ technology focusing on leveraging automation and robotics in 3D printing platforms for faster, economical and sustainable construction methods compared to conventional technologies [25]. This can be a new I 4.0 approach to solve the issues of mass housing for rural and urban poor. Additive manufacturing and its experiments are under development and its application to field of civil engineering and architecture are also being experimented. Linear CDW inert waste generated out of conventional demolition systems can become the raw material for additive manufacturing. For this process binding materials like recycled single use plastic waste need to be experimented with other composite materials. These building components need to be designed as modular systems and they need to be designed for disassembly. This kind of combination of inert CDW material and plastic waste can be used for production of modular building elements which can be assembled into shelters. Industry 4.0 technology can be used for quantification of upcycle of materials and in reward, green incentives need to be credited to PP. After this let us look at the D-tools, followed by CE, its linkage to CDW and its impact on the environment.
Table 2.
Circular Economy and Construction Demolition Waste
(CE) and Construction Demolition Waste | |
![]() | Micro level waste generated is due to de construction of one or more products. Meso level is the area of one neighbourhood affected by deconstruction, example is TOD areas along metro corridors. This is all along the length of mass rapid transit systems in all cities. Macro level implications are the environmental, economic impacts that are generated at the scale of entire region. In the context of Pune & Mumbai this impact can be managed at regional planning scales. With the help of I 4.0 - Linear economic model can be converted to CE model. |
Circular supplies Business models based on supplying fully renewable, recyclable or bio-based resources as alternative to single-lifetime inputs [51] | Pre-Industrial revolution practices were CE based, subsequently in each IR, industry practice was driven by mass-communication and advertisement that had influenced urban and rural areas as well. Due to this, use of cement and its products usage had increased. The major barrier and key issue is with excess use of cement, and cement concrete-based elements as these products increased CDW. |
Resource recovery Business modelsthat recover useful resources or energy out of disposed products or by-products and thus transform waste into value [51] | Barrier is about lack of awareness about CE at Central, State Government, and PP level. Current approach of product development – product’s design thinking is linear economy based, right from conceptual design to end of the life of the product. |
Product life extension Business models that extend working lifecycles of goods and materials by reselling, repairing, refurbishing, remanufacturing and repurposing of products [51] | PPs are not worried about the afterlife of disposed components of the product as their life is 30 to 40 years. Earning maximum profit and saving time is their first priority. Resources are taken for granted and they are assumed to be available for ever. CE, Education and awareness is required. |
Sharing platforms Business models that promote a platform for collaboration among product users (individuals and/or organisations). The platforms enable increased utilisation rates by facilitating shared use, access or ownership of products [51] | Lack of awareness about “designed for dis assembly” systems, I 4.0, BIM, in the design is the barrier. CDW Management issues are addressed through linear economic waste disposal systems or partially adopted CE at local level, this approach does not help to address the issues of CD waste. The issue of CDW exists at micro, meso and macro level and we cannot address this issue by linear economic model i.e., by setting up of construction waste treatment plants. Pune has got one at Wagholi |
Product as a service (PaaS) Business models that offer product access, instead of ownership, to customers. Businesses retain ownership of the products, while products are used by one or many customers through a lease or pay-per-use arrangement [51] | Indian psychology of owning the premises for residences and businesses are one of the major barriers and this might take a long time to change or might not change also. While purchasing the product, it is assumed that the ownership will remain for generations with the family. Cultural values might change after economic growth, because at present immovable assets are considered as income sources for post retired life. On the other side public owned built spaces or open spaces are very less, ill maintained, vandalism of many elements is often seen in public spaces. |
Urban Planning – RP, DP & TP
Central Government’s (Niti Aayog’s) policy document promotes vertical high-rise high density growth for Indian Cities. It states that “Indian cities have focused on horizontal growth for far too long. It should now focus on vertical growth” [26] and suggests various measures, one of them being “provide considerable rewards to cities that relax their floor space index (FSI) norms. One of the key reasons behind India’s horizontal sprawl is stringent FSI norms. The discussion on changing FSI norms considering trunk infrastructure and other social issues needs to be expedited across India” [26]. India being democratic country and it is formed by various states, union territories and as the part of governance urban development falls under the state subject i.e., Government of Maharashtra under Maharashtra Regional and Town Planning Act of 1966. Under section 21, local authority can prepare, submit and sanction the development plans and implement them [64]. For implementation of Development Plans, Town Planning Schemes can be prepared. For that state government needs to accept the inevitable process of urbanization and convince the farmers about the rewards and appreciation they will individually get after conversion of agricultural land to urban land. Vested political interests always discouraged farmers to convert their lands in to well infrastructured urban land. That has resulted into very densely packed urban residential and mixed-use developments where farmers have subdivided their large holdings into small affordable plots in the range of 100sqm which end users could afford to buy and “as per the Gunthewari Act, the practice of creating small plots of agricultural land in multiple gunthas (1,089 sq ft area) was illegal and hence, carrying out constructions on gunthewari land was also illegal. In the year 2001 State government introduced The Maharashtra Gunthewari Development (Regularisation, Upgradation and. Control) Act. It was applicable to areas on the outskirts of a municipal corporation and city boundary limits for regularisation of gunthewari constructions till 2000” [27] On these small pockets, migrated population executed mixed use developments. At many places these plots and houses were sold to the unaware users where development plan road widening, and other DP proposals were going to affect the properties. Eventually all these properties which are abutting to development plan roads got affected by demolition actions. Legal notices were served to these properties and they were demolished. At many places, where these houses were not affected by DP proposals, they were legalized under guntehwari scheme. Failure of implementation of DP & TP Scheme mechanism is another reason for generation of CDW. As against that, Gujarat government has used two stage urban planning process known as DP-TP mechanism and that has shown good results. The first stage involves preparation and ratification of a strategic, city-wide Development Plan. The second stage involves preparation and implementation of one or more TPSs to realize proposals of the Development Plan [28]. Gujarat state prepared the Development Plans for various urban local bodies under Gujarat Regional and Town Planning Act and implemented Town Planning Schemes as well. This kind of urban land management techniques could have helped to facilitate the IRs and managed urbanization process and CDWM could have had a direct and Indirect impact because of it. Though all these provisions were there, Maharashtra state lacked in vision and political will to implement it. Master Planning failure created more CDW.
Background
Arts, crafts, culture, people, architecture, urban spaces, settlements, CE, IR & de construction, and tools for de construction are all diverse terms but they are linked to urban transformation. It would be interesting to look at these terms in the context of construction industry, SDG12 i.e., responsible consumption and production and climate change actions.
Study Area – Pune City region, Industrial Revolution’s impact
Pune city is located at 18° 25′ N and 18° 37′ N latitude to 73° 44'E and 73° 75'E longitudes and at an altitude of 560 m, above mean sea level on the eastern slope of Sahyadri hills in Pune district [29], It is located in Maharashtra state in India (Refer Figure 5). Pune city and its urban sprawl has enjoyed challenges of all IRs that took place i.e. I 1.0, 2.0, 3.0 & 4.0 (Refer Table 3). State Government made their best possible attempt to facilitate all these IRs by providing land, infrastructure, housing and manpower. Pune has the potential to become the epicenter of Industry 4.0 adoption and be a provider not for Indian market but also for global markets with its vibrant manufacturing industry, IT and engineering services industry, premier research institutes, start-up hub and enabling organizations and programmes, said the Mahratta Chamber of Commerce, Industries and Agriculture (MCCIA) and QLEAP Academy report on Industry 4.0. The city has a perfect amalgam to lead in the fourth industrial revolution and become a major hub in India [30]. The key details of the urban development and industrial development authorities, and their relations with the IRs are given below in the chart format.
Table 3.
State Governments efforts to facilitate the Industrial Revolutions (Broad numbers are given)
Government of Maharashtra’s contribution for Facilitation of Industry 1.0 To 4.0 | |||||
Sr.No | Name of Authority | Area in Ha | Remarks | ||
Facilitation by State Government | |||||
1 | MIDC Pimpri | Maharashtra Industrial Development Corporation Pimpri | 1224 [53] | The first industrial unit to come up alongside the Pune-Mumbai freeway was the Hindustan Antibiotics manufacturing facility in Pimpri in 1955. Followed by Huffkin Institute, Tata motors and Bajaj industries. These units were supported with 14000 to 15000 original equipment manufacturers, that is how city had responded to Industry 1.0,2.0 [54] | |
2 | MIDC Hinjawadi Known as Rajiv Gandhi infotech park | Maharashtra Industrial Development Corporation Hinjewadi | 556 | Industry 3.0 and Industry 4.0 companies are located in these areas – to name the few, in Phase I – Infosys, Wipro, KPIT, etc Phase II – Infosys, Wipro, Phase III – KPIT, Tech Mahindra, Cognizant etc Phase I + II + III total area 96.42+236.23+223.56 = total of 556.21 Ha [55, 56, 57] | |
3 | MIDC Chakan | Maharashtra Industrial Development Corporation Bhosari | 1436 | General Electricals (GE), Bajaj Auto, Bharat Forge, RPG, VW, Mercedes Benz, JCB, have already developed their plants equipped with Industry 4.0 in Chakan [58]1436.15 Ha total area is acquired in phase II | |
4 | PMC & PMRDA* | Pune municipal corporation | 6914 [31] | Pune city has DP for old city limits, 23 villages which have bio diversity park (BDP) provision, Yeolewadi, 11 villages merged in 2017 and the latest for newly added 23 villages. [59] * Pune Metropolitan Regional Development Authority | |
5 | PCMC | Pimpri Chinchwad municipal corporation | 8451 Ha | This area is for newly added 18 villages in the new DP area of PCMC [60] |
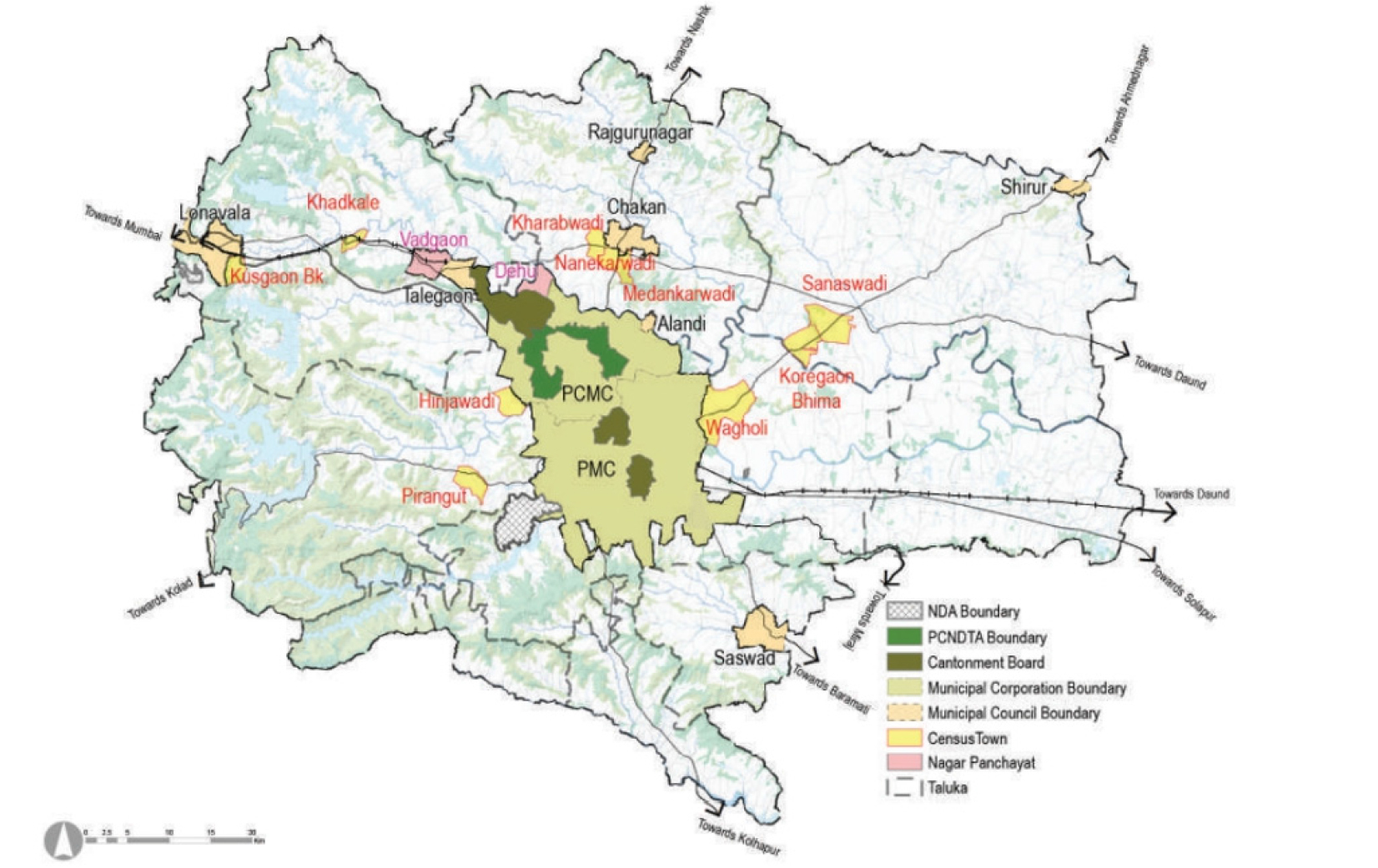
Figure 5.
Study Area – Pune Metropolitan Regional Development Authority, Maharashtra, India. Source: [48].
Table 4.
Transit Oriented Development (TOD) in India – Urban Transformation & CDW is expected in this region
The above chart does not include the major contribution of built spaces that are contributed by private real estate developers in the form of townships, Special Economic Zones (SEZ) etc. The historic city of Pune is an educational hub, known as Oxford of east and is very well connected to Pimpri Chinchwad Municipal Corporation (PCMC), Maharashtra Industrial Development Corporation MIDC’s developed at Pimpri, Bhosari, Pimpri Chinchwad New Town Development Authority (PCNTDA), Pune Metropolitan Regional Development Authority (PMRDA). Amongst them PMRDA engulfs all the other authorities and helps to facilitate conversion of agricultural land to urban land. PMRDA in its draft development plan has proposed 26 town planning schemes, 59 public housing projects along with network of 10 metrorail routes, high-speed railway and crescent railway and two ring roads [31]. Implementation of this draft plan may help in responsible consumption and production of resources (SDG 12) by avoiding CDW. Transit oriented development (TOD) on 10 metro rail routes will have a FSI of 4.0 and will attract major urban transformation and may generate humongous amount of CDW. If we scale the problem of CDW at national level and look at TOD length then summary length is attached in the chart (Refer Table 4).
Materials and Methods
What is done in the research
Through the literature review, pre industrial and post-industrial revolution CD tools were reviewed (Refer Figure 6). The tools and their effectiveness linked to the latest technology of each Industrial Revolution and it’s effectiveness in management of CDWM was confirmed. Linear economic and Circular Economic CDW management practices and its linkage to technology are assessed. The resource management review is done for upcycle or down cycle of resources. In the context of Global Warming, Issues of poverty linked to Global South & Indian regional Context, CDW management, Industry 4.0, CE and its integration was reviewed. Jobs creation, green jobs, role of Mirco small and medium enterprises (MSME)s, green economy in the construction sector with I 4.0 integration possibilities are explored. CDW management practices and its conversion to CE is reviewed. Possibility of green jobs creation at regional, city and individual buildings scales for transforming construction industry to green economy is reviewed. I 4.0’s additive manufacturing technology and generation of green jobs and green economies through MSMEs are explored. Possibilities for reuse, recycle, and repurposing the resources, products and their components are reviewed. Preparation of de construction plan with PP, with a modular approach, testing, retrofitting, cloud-based data management, and use of I 4.0 can help to manage the CDW through a CE, and has scope for further research.
How the research tests/experiments/surveys/case studies are done-
References from various secondary sources like books, journal articles, government acts, You Tube clips, & newspaper references are used as evidences for the analysis, results and then further used for drawing conclusions (Refer Figure 6). It starts with example at regional scale for infrastructure project, CDW management works in Global Bio diversity hot spot in Western Ghats, this is taken as the case study. Evidences are gathered from Google Earth images with time lines, owner’s own evidences of illegal dumping in the valley are documented through images and scientific data to show the impact on ecology. At the City Scale and Town planning schemes scale, two local governing bodies with their TOD areas and its urban transformation impacts are studied and scaled to national level issue of CDW management. This helps justify that there is a need of CE policies for CDW management at national level. The gravity of the problem is defined with the quantum of CDW that is going to be generated after implementation of TOD policy. At architecture scale, that is at micro scale of CE, the demolition tools are rated for its results and outcomes. The tools which help to retrieve more resources through deconstruction are rated as CE tools and rest of the tools are rated as linear economic tools. The process of demolition, primary survey for it etc are kept out of the scope of this paper. The paper concludes with recommendations for transition to CE at macro and meso scale, and micro scale work is descoped from the paper.
Tests and Results
Regional Planning
Proximity to Mumbai, good climate, good quality educational institutes and skilled manpower are the few reasons because of which Pune region saw all industrial revolutions. At present Mumbai and Pune region are experiencing I 4.0 transformation due to information technology, robotics, machine learning and their applications. These are getting widely used in various industrial units like Bajaj Auto, Bharat Forge, General Electrical, Henkel Adhesives Technologies India etc and also in the medical fields. The city can build on the capabilities of data science, analytics, IT and become a hub for cognitive systems, build Industry 4.0 talent factory, create entrepreneurs in 3D computer simulations, rapid prototyping, IoT, 3D printing, AR, cybersecurity, cloud and robotics [30]. I 4.0 provides an opportunity to gather, store, analyze and use lots of data and information simultaneously. We need to use this technology in the interest of environmental protection. The industrial world is facing rapidly changing challenges. Our resources are finite, and we all need to do more with less. Digitalization and automation are the game changers to meet these challenges on the way to Industry 4.0. It is essential to collect, understand and use the massive amount of data created in the Industrial Internet of Things (IIoT). The Digital Enterprise is doing exactly this by combining the real and the digital worlds. As a result, the infinite amount of data allows us to use our finite resources efficiently and with that make the industry more sustainable [32]. Recently, deep learning started to be used to detect and identify waste in natural environment with drones or cameras mounted on vehicles [33] The CDW management solution for Mumbai, the commercial capital of India, and Pune, the cultural capital, is in combining I 4.0 with (CE) at macro, meso and micro scale. Each IR’s early impacts were experienced by Mumbai and then they were quickly followed in Pune. Amongst the many environmental impacts, generation of CDW poses a bigger challenge in urban and peri urban areas. CDW and its worst impact can be seen in illegal dumping in water bodies in Mumbai & Pune and that leads to flooding of cities. We need to change our perspective from linear to (CE) and address this issue at various scales i.e., regional planning, City Planning, Urban Design, Architecture and Interior Design scales so that we can address the issues at a macro, meso, and micro scale.
Table 5.
Regional Imbalances, Circular Economy and Opportunities for CDW management
Indian Sea Ports and Global South opportunities | Remarks |
![]() ![]() |
CDW management, Industry 4.0 and CE can be used for Planned de-construction with modular repurposing of the building elements. |
Source: [34, 35] | |
![]() ![]() |
Sea Ports interlinked, Dedicated freight corridors by Indian railways can be a green economic solution and will help to address economic imbalances. |
Source: [24, 36] |
Mumbai and Pune can be envisioned as large urban agglomeration and in another 50 years’ time it will get developed like that. For absorbing the impacts of IRs, the state government took various actions like planning of Navi Mumbai City, setting up of MIDCs, PCMC, IT & ITES software parks, SEZs, as industrial hubs. At the same time “the poor operating condition on national highway 4 (NH4) made it necessary for the Maharashtra Government to build an independent toll expressway, as this travel corridor represents the economic backbone of the region [37]”. Because of limited land in the Island city of Mumbai, growing urban pressure, and excessive industrialization, the government explored the opportunities in tier two cities, which led them to focus on Pune. The biggest challenge was to reduce the travel time between the two cities by road way connection, because it was passing through Western Ghats (Refer Table 6). The Maharashtra State Road Development Corporation (MSRDC), an agency of the state Govt. built the Mumbai Pune Expressway (MPEW), a six-lane facility with high design standards in (year) 2000 and was authorized to collect tolls from road users [37] This MPEW passes through the Global biodiversity hotspots known as Western Ghats. Prof Madhav Gadgil’s committee defined ESZ16)1, ESZ2, ESZ3 for protection of biodiversity in eco sensitive zones in the Western Ghats, by treating them as shock absorbers. As per the report ESZ1 zone is the most sensitive zone and, in this zone, “Avoidance of expressway and new highways [38]” is mentioned. For ESZ2 “upgradation of roads possible/permitted subject EIA17), strict regulation and social audit [38]” is stated. For ESZ3, nothing is defined. One of the reasons for formulation of this kind of policy could be the case study that is enclosed below.
Table 6.
Case Study CDW Management and Global Concerns
Case Study – Western Ghats India – CDW Management Issue @ Khandala -World Bio di-versity Hot Spots – Biodiversity falls below ‘safe levels’ globally, Levels of global biodiversity loss may negatively impact the ecosystem function and the sustainability of human societies, according to UCL-led research dated 14 July,2016. In the UN Environmental Programme World Conservation Monitoring Center (UNEP-WCMC) at Cambridge, Dr Tim Newbold from University College London quoted, “We know biodiversity loss affects ecosystem functon but how it does this is not entirely clear. What we do know is that in many parts of the world we are approaching a situation where human intervention might be needed to sustain ecosystem function.” |
![]() |
The author had an opportunity to work on a five-star hotel project. This project site was affected by CDW dumped during execution of Mumbai Pune Express High way. The waste was generated due to execution of six tunnels on the express way and it was dumped on the Hotel Project site. Due to this CDW dumping, the hotel project had to be abandoned. The results are documented with the permission of owner and their name is not disclosed. |
Extent of Eco sensitive area of Western Ghats in India- stretches to a length of 1490 km from Tapi Valley in the north to Kanyakumari in south. With an area of approximately 129037 sq km, it stretches to a width of 210 km in Tamil Nadu and narrows to as small as 48 km in Maharashtra (leaving the Palghat gap) [38]. Map and Chart showing details of Western Ghat (Source [38]) ![]() ![]() UNESCO has included certain identified parts of Western Ghats in the UNESCO World Natural Heritage List because Western Ghats is a Centre of origin of many species as also home for rich endemic biodiversity and hence a cradle for biological evolution [62] |
The author came across two contradictory experiences about management of CDW. First one is a personal interview with one of the project engineers who had worked on this expressway project and second was author’s own association with execution of a five-star hotel (Refer Table 7). During discussion with identified engineer, he confirmed “that all the excavated materials from tunnels or road works i.e., hard stone basalt, soft stone(murum), and soils were repurposed for road construction work for cutting and filling works. This was mandatory design clause for the execution works and it was part of the contract.” That was the part of the guideline defined by consultant and was to be followed by contractors. And the said engineer confirmed that this was adhered to. To the contrary, the author came across another case study in which exactly opposite was done. The excavated materials like stones of various sizes and debris were dumped into a valley (Refer Table 8). For that we need to understand the term lead- it is the horizontal distance travelled by material from center of excavation to center of disposal point. Lift is the vertical distance travelled by the material from place of demolition to spreading of heap at final destination. In the coming pages, the author has enclosed evidence to prove that if infrastructure project’s CDW is not managed properly, it can create larger environmental impacts. Western Ghats in India is a sensitive ecosystem and it is a part of larger global biodiversity hotspots. Policies related to management of CDW cannot be linear and they need to be framed from CE perspective, with the help I 4.0 technologies.
Table 7.
Case Study – Impact of CDW Management at Micro Scale
Case Study - Global Bio-diversity hotspot and CDW Issues (Location: Latitude 18°45'41.88"N and Longitude 73°22'57.70"E) | |
![]() Overall context - Mumbai Pune Expressway and Western Ghats Source: [37] | ![]() Proposed Five-star hotel site shown in Yellow – Location is close to water fall. |
![]() Contour Plan with Bore Hole locations of Geotechnical Investigations report summary shows that out of 13 bore locations, bore no. 5,6,8,10,13 defined by pink area had average filling of 20.0m. This was CDW generated out of tunnels construction and dumped into the valley. | ![]() Geotechnical Investigation sample one result attached, rest are available with author |
![]() | ![]() |
Conclusions - Owners of the property had invested in the land for developing five-star property on the hill top, with building permissions of local governing authorities. The site was on a CDW hill top (generated after the execution of Mumbai Pune Express Highway). Due to this issue, scenic view was not available and the project had to be abandoned. Note: All images are reproduced with the permission of owners unless specified. |
Table 8.
Case Study – Impact of CDW Management at Architecture Scale
Urban Planning and Urban Design
Due to industrial revolutions, the global south always struggled to cope up with the pressure of urbanization. City planning always lagged in catering to the pace of IRs and urban development. Each IR generated new economic activities which created the demand for housing, and urban local governments were not equipped to handle industry requirement of well-planned industrial lands with good physical infrastructure like airports, road, electricity, IT services etc. In Maharashtra, the MIDC (Maharashtra Industrial Development Corporation) was created to support all IRs but during this process of planning and implementation, a lot of CDW was generated due to demolition of rural houses and other supporting built structures. In India, land is owned by individuals, the government, semi government authorities, private companies etc as against few countries where land is owned and controlled by the government. But in India, the majority of the land is owned by farmers and its present use is agriculture. Conversion of this agricultural land to urban land-use in a democratic manner is a politically driven process. For better facilitation of urban land, politics plays a key role and the politicians become the bridge between rural and urban population. They need to strike the balance and shall not focus on people as only potential vote banks to get elected and remain in power for long terms. Maharashtra started really well by supporting the IRs but later on political will was missing for showing the vision for urban development. The state government missed the opportunities to implement a DP-TP Scheme mechanism. Best of rural to urban land conversion is possible without losing original plot owners’ land ownerships. Maharashtra state did not believe in MRTP Act of 1966 and did not implement the Urban Development Plans with the help of DP-TP Schemes mechanism. Town Planning Schemes are the scales where detailed design of streets, utility corridors, and public areas are designed at an Urban Design scale. In 2014, Smart cities mission was under taken by central government and part of the funds were used for cosmetic changes in the public spaces. Earlier un planned, un-designed, and un-detailed areas are partially getting augmented, leading to more CDW. Core issues related to city structure, mass public transportation networks by metro, BRTS systems, and urban infrastructure are imposed as the surgeries to address the local issues (Refer Table 9). This is linked to failure of Urban Planning and Urban Design process. Due to these reasons, more CDW is generated in cities, neighborhoods, and communities, which are not planned with considerations of impacts of Industrial Revolutions. Democratic model of DP – TP schemes implemented by state of Gujarat proves to be a good urban development model and can lead to reduction of CDW. TP Schemes are more democratic systems of urban land management and politicians need to accept this and reach out to farmers to convey to them the pros and cons of TP Scheme and help them convert agricultural land to urban land. Politicians should not look at private developers as partial source of funding option to lay city infrastructure like – roads, drainage, electricity, telecommunication lines on developer’s expenses. This kind of piece meal development done with the help of only Development Plan leads to more CDW due to reworking of uncoordinated urban infrastructure. CDW and its example is shown through transit-oriented development TOD in Pune region.
Table 9.
Transit Oriented Development and CDW – Issues impacting at Meso scale
Case Study - Transit Oriented Corridor as the CDW generator (PMC & PCMC Areas) | ||
![]() | TOD – Zone for Pune Metro line-3 from Civil Court, to Hinjawadi to Maan, total length 23.33 km and 23 stations passes through PMC & PCMC. As per the TOD policy, 500m to 800m zone on either side of metro is proposed with additional Floor Space Index (FSI). In the near future due to urban transformation, major demolition activities are expected for consuming additional FSI. | |
![]() | ![]() | |
![]() | ![]() | Proposed part of Development Plans of PMC, PCMC and Google earth image’s white and yellow boundary show the TOD area. Figure 5 shows private developers dark blue land- use of Industry 4.0 development forced the metro alignment to change the route and pass from this area. Lots of plots are linear in shape and internal Town Planning scheme roads are missing. |
![]() | ![]() | |
![]() | ![]() | One of the major reasons of CDW is unexpected challenges of I 4.0 and State Government is not prepared to tackle the Urban Planning and transportation planning issues |
Top image - Demolition of bridges and flyovers because of unplanned development, IT luxurious offices | Coexistence of CDW, dumped in the river bed, and Private I 4.0 high end development. |
Architecture and Interior Design
I 3.0 and I 4.0 helped in the development of information technology parks with IT & ITES complexes. High-rise high-density housing development projects catering to the needs of housing was a by-product of that. Major cities in India saw this transformation and impacted cities were Mumbai, Bangalore, Hyderabad, New Delhi, Noida, & Pune. Private developers had major contributions in creating the built spaces and public infrastructure of road, water supply drainage, and electricity provisions as state government’s efforts were not sufficient for supply and management of well infrastructure urban land. At various locations, special townships and mixed-use developments were planned and executed by private developers who accommodated IT & ITES complexes in them. In Pune region, few examples of well planned and executed townships for supporting Industry 3.0 and 4.0 are Magarpatta City, Amanora City, MIDC Hinjawadi, where major IT and ITES complexes were developed and they could cater to urban infrastructure for IT companies like Infosys, Cognizant, TCS, Tech Mahindra, L & T etc.
The notion that parts of buildings may be changeable and/or adaptable is not new. The concept of “Open Building”, introduced in the early 1990s, advocates that a building is a construct of structural components as well as replaceable, reusable and movable infill [6] This statement stands true for building’s designed before IR, which could be disassembled in a better manner, recovery of resources was far more and they could respond to local arts, crafts, materials and culture which is an integral part of architecture (Refer Figure 7). As IRs progressed it clearly shows that building, its envelops and structure started becoming more rigid and homogeneous, due to that it generates more CDW. Residential buildings are using RCC construction systems and they are not designed for disassembly. The current use of tools generates linear CDW and demolition process reduces materials into debris and that does not help the CE. Commercial architecture is influenced by Western Architecture where glass façade, cladding etc are used. “Based on such a notion, the types of building components with the most potential for disassembly, exchange and reuse include framed glazed systems, ceiling systems (“space”); lighting and air handling systems (“services”); and façade systems (“skin”) [6].” PPs need to relook at I 4.0 and green practices as an opportunity to design it for multiple life cycles. Disassembled structural components could be 30 to 50 years old if they are retrofitted and upcycled, which will have a positive impact on the environment. “Countries such as the Netherlands have established targets for a fully CE by 2050, including the construction industry; this has led to an increase in the introduction of “platforms” such as Madaster and BAMB (Buildings as Material Banks) to identify and facilitate the reuse of components from existing buildings [63].
Pace of urbanization, urban planning and its implementation creates more CDW because later is politically driven and it is slow paced. This is directly impacting environmental degradation because more CDW is being generated. Traditional construction materials before introduction of cement and mild steel in Indian market were Wood, stone, mud bricks, burnt brick masonry and lime. Houses were executed on modular construction system and the built spaces could be assembled/disassembled. Due to this after de construction, building components could be retrieved. Value of building materials via the “material passport” concept and pursue the idea that every building is an “adaptable platform” and a “material depot” [6] was possible. During this period resources were getting used in a more effective manner and built spaces were responding to climate and socio-cultural needs of society. After IRs, due to urgent need of housing cement, use of steel started increasing in urban areas and multistoried reinforced cement concrete buildings were developed. The products, if scientifically de constructed with the help of architects, structural designers and (CE) tools (D-Tools), can be repurposed at the macro scale. Modular designed deconstruction followed by (CE) approach of upcycling of modular products at macro scale is the future. For this purpose, I 4.0 along network of ports and Indian railways freight corridors can be of help to the rest of India. Countries in the Global South like Sri Lanka, Bangladesh, Nepal, Afghanistan, & Pakistan can also be supplied with modular building components/materials for housing. Upcycled modular structural elements need to retrofitted and certified by various civil engineering institutes of national repute like Indian Institutes of Technology, National Institute of Technology, etc. With the help of data science, the product information of these retrofitted structural elements can be retrieved from cloud and the components can be reused.
Preferred Circular Economic Tools for Designed Disassembly
As the IRs progressed CD tools also got transformed from manual energy to other types of energies like chemical, thermal, electric, hydraulic, pneumatic etc. A wide range of tools are available, including small impact hammers, drills, saws, and grinders for deconstruction (Refer Table 10) [39].
Table 10.
Circular Economy rating for construction demolition tools
Construction Disassembly Tools, Machinery, Technology & Industrial revolutions Criteria for analysis of D-Tools: 1. It is assumed that sole criteria for selection of the disassembly tool is left to designer and other parameters for the use of tools like – energy, time, cost and manpower do not affect the analysis. This might help us to understand the new use of tool in the context of Industry 4.0 & CE. 2. Circular Rating criteria – A, B, C & D where A is good and D is the worst rating. 3. Rating of tools – Tools that work on principles of CE to upcycle the product and its elements in CD process are rated with A and tools that works on linear economic principles and downcycle the product, its elements in disassembly are rated as D. In the rating process A is highest and D is lowest. 4. It is assumed that PPs are aware of (CE) and they are consciously selecting the tools for upcycle of resources i.e., 3 Rs – Reduce, Recycle and Reuse 5. Tools are selected as per the disassembly of project, and construction disassembly plan is prepared by PP with the sole objective to move towards CE and upcycle the disassembly process. 6. CE and objective of conserving the bio sphere and Techno sphere is the sole purpose. | ||||||
Period | Tools, Machines, Technology used for demolition. | Energy type | CE Rating | |||
Reduce | Recycle | Reuse | ||||
Post - IR |
Prybar, Bush Hammer, Sledgehammer, drills, points, Chisels![]() | Manual Energy | C | A | A | |
Post - IR | Drop Hammers / Blades - Hydraulics powered are used to demolish concrete highway pavements, parking lots, and other slabs on grade [39] Verylimitedupcyclepossible. | ![]() | Hand Operated Hydropneumatics | A | C | C |
Post - IR | ![]() |
Hydraulic/pneumatic impact hammers- hydraulic pressure for removing small areas of hardened concrete. Works with Hydraulic pressure, number of impacts and weight of needle are an important parameter. Very limited upcycle. | Hydraulic/Pneumatic pressure is used | A | C | C |
Post - IR | ![]() |
Spring Action Hammers - Used for breaking concrete pavements, decks, walls, and other thin members, faster than hydraulic hammers, truck mounted with rubber wheels helps for movement from various sites. | Arm is Hydraulic powered and Spring powered impact head | A | C | C |
Post - IR | ![]() |
Rotating cutting heads- inline single drum works like large drill where the drum for the in-line cutter head rotates around the axis of the boom. The drums are available with flat or rotating conical bits – Used for concrete removal in deck slabs etc. | Hydraulic Powered | A | C | C |
Post - IR | ![]() |
Rotating cutting heads- Functions in the same way as mentioned above – difference is there are two drums that are attached which are used for removal of concrete in deck slab. | Hydraulic Powered | A | C | C |
Post - IR | ![]() |
Resonant frequency breaker, Self-propelled, four-wheel rubber-tired power unit that uses resonant beam technology to apply energy through a high-frequency resonant impact breaker to break the concrete pavement | Resonant beam Technology | A | C | C |
Post - IR | ![]() |
Non explosive agents – chemicals like proprietary mixtures consisting primarily of calcium oxide and calcium silicate is mixed with water, poured into predrilled holes, and after a period of time, the mixture expands and exerts an expansion force sufficient to crack the concrete [39] | Chemical energy | A | C | C |
Post - IR | ![]() |
Stitch Drilling- is the technique of drilling holes next to each other in such a manner that it creates the required opening in concrete | Electrical | C | C | C |
Post - IR | ![]() |
Explosive Blasting - Blasting has been used for complete building demolition and for underwater demolition, The technique requires a licensed worker and controlled blasting techniques to maintain safety and minimize damage to the concrete that remains and the surrounding environment. Blasting mats are used to minimize fly rock, and textile fiber mats are used to lower dust and noise levels [39]. | Chemical explosion, high temperature generates collapse. | A | C | C |
Post - IR | ![]() |
Drills and Saws – Done with the help of hard cutting diamond tools. Hard aggregate and steel in concrete may reduce speed of cutting. Water jet, compressed air or nitrogen is used for cooling, this can allow cutting in vertical and horizontal planes as well. | Compressed air, hydraulics, or an electrical system | A | A | A |
Post - IR | ![]() |
Diamond wire saw - A diamond wire saw is a continuous loop of multistrand wire cable strung with steel beads bonded with diamond abrasive that is pulled through the concrete [39] First, aholeis drilledandthenthediamond wireisrotatedonapulley withpower. | Shear cutting, electrical power driven | A | A | A |
Post - IR | ![]() | Mechanical or hydraulic splitters are placed in predrilled holes, with the splitting action developed by a steel plug or wedge positioned between two hardened steel shims or feathers, at least one side need to be open [39]. | Through wedges inserted in the member | C | C | C |
Pre-Industrial tools and few post-industrial tools like Dimond cutter and diamond saw can be called as CE tools and need to be used along with I 4.0 technology |
Covid 19, Industry 4.0 and Society 5.0
For avoiding spread of Covid-19, Central government and State governments in India adopted social distancing measures. For that, full and partial lockdowns were implemented in the period of two years starting from 25th March 2020. With the help of I 4.0 and Society 5, Indian urban and rural areas adopted to the crises. During this time, use of robotics and artificial intelligence had increased and essential services were supported by I 4.0 technologies. Health sector was stressed and there was a tremendous shortage of human resources, hence, various experiments of robotics were done at the time to assist medical professionals. At the same time, experiments related to solid waste management for medical waste segregation could have been explored with the help of machine learning. “One of the ways to support waste sorting is machine learning (ML). In recent years -ML-based systems that can support or fully cover sorting processes were implemented, accelerating this procedure as a result. The most commonly used solution includes smart self-sorting waste bins, which are capable of classifying one object located on a clear background at a time [33]” This was the opportunity for managing medical waste. Partial lockdowns means - sectors which were incorporated under essential services sector were allowed to access the public spaces, public amenities can move within urban and rural areas. In that, building construction and city infrastructure development activities were excused and construction execution sites were allowed to carry on their regular activities, provided that they followed the strict guidelines issued by government. Construction industry took this as an opportunity and priority CDW were under taken. Major public infrastructure projects on express highways and major arterial roads were reviewed and priority CDW was undertaken and finished. During normal situation this was not possible due to heavy and constant traffic. Demolition of Amrutanjan bridge on Pune Mumbai expressway, Demolition of flyover at Pune University Circle, Expressway repairs and maintenance works taken up by MSRDC etc. are the examples which can be further researched. Similar kind of pattern was observed in interior design renovations - lot of busy restaurants, hotels and cafeterias in cities got renovated because the businesses were forced to shut down and construction activities were allowed as a part of essential services. This forced closure gave the opportunity to all these business houses to renovate and redesign but this also impacted the CDW, quantification of all these situational impacts in increase in CDW is a separate area for further research works. This pandemic- lead urgency created new models of work – complete work from home and hybrid model of working i.e. to work for few days at home and few days at office. IT & ITES industry and majority of service industries very well adapted to both these models. Educational Institutions were closed initially and later on education sector also adopted online teaching learning methods and their outcomes are under debate. This forced PPs to relook at the earlier conceived products and redesign them for the new requirements. Suddenly there was a surge in 2.5/3 BHK apartments in the areas where I 3.0 and 4.0 had more impacts because individual houses had to be used as work places and one extra room was needed for that purpose. (PP)s changed the product brief and reworked on it to adopt the under-construction projects by partial demolition/full demolition. This is a separate area of work and can be further probed into. Till today, industry is not able to come to terms with the pandemic and Industry 4.0 sector is still working in hybrid mode. If the industry accepts this as the new normal because it has benefits to the employer, employees, citizens, and cities, then this will be a big transition in city and regional planning and extensive research is happening in this area. Repurposing of existing office buildings and building complexes, constructed for IT & ITES which were partially occupied for the last two years, is now going to be the major challenge. Many of these are rental properties and they are vacant because business models have changed and there is very less demand for rental spaces. At some point of time, they might generate CDWs as well, thus, when a building approaches the end of its life, these resources could be identified, retrieved and exchanged with another user, enabling their circularity and reuse [6].
Conclusions
All IRs offered opportunities for economic and social growth but they have affected the environment adversely. Industry 4.0 offers unique opportunity to relook at SDG 12 i.e., responsible consumption and production from CE perspective and save the planet earth from further degradation. Advancement of technology gave us tools and machines which can produce products in a quick time frame, but that gives more responsibility to (PP)s. ‘D-Tools” need to be planned for use along with the help of I 4.0 & CE so that resources can be used properly and very less waste is generated. For that, we need to adopt the circular strategy. PPs need to be responsible for designing the construction product, right from conceptual design of the product to end of the life of the product and its regenerated materials. With the help of I 4.0, the product and its components shall remain traceable during and after the end of its life. Design for disassembly, I 4.0, and CE shall be the future direction for construction industry and use of cement and cement concrete need to be adopted for this purpose because at present maximum construction activities happen with these materials. For management of CDW waste – the strategy of each local governing body managing its own CDW within its own jurisdiction is too defensive and of a linear economic approach. Existing regional imbalances, advancement of data sciences and I 4.0, offers us many opportunities for CE and with CE these challenges can be addressed in a better manner. Supply chain management, gig economy, green jobs, green economy, and skill development are the few opportunities hidden within it. Little tweaking in the Regional Plans, Development Plans can help us to create I 4.0 industries and Green SEZs which can repurpose the modular components from CDW. The small and medium enterprises constitute an important segment of the Indian economy. This sector is a “nursery of entrepreneurship” and contributes to about 8% of the GDP, 45% of the manufactured output and 40% of exports [40]. Author Gurudas Nulkar argues that as major industrial business houses in India are getting transformed to green economies in production sector, the construction demolition contractors, formal or informal, should get registered under MSMEs and need to transform their businesses to green economies. In this, construction industry has a very long target to achieve and it will start from education and awareness. After TOD development, CDW will become a national level environmental challenge. At the same time, it is an opportunity to utilize CDW resources after modular retrofitting. While formulating & implementing the policies linked to CDW, extreme care is required. Most advanced I 4.0 technologies should be used for avoiding misuse and unwarranted activities linked to CDW management & further environmental degradation.
Further Works
Industry 4.0 along with additive manufacturing i.e., 3D printing, can reuse and repurpose various building components. Indian startup Tvasta 3D printing offer raw material flexibility– utilization of eco-friendly materials [41]. Powdered construction demolition inert waste materials can be repurposed for green economy and green jobs can be created. These CDW materials are going to be available in plenty and can be repurposed. These inert materials need to be further experimented with current 3D printing’s current raw materials like polycarbonate, polylactic acids, polyvinyl alcohol, ceramics like zirconia, alumina, tricalcium phosphates, biomaterials like silicon, zinc, calcium phosphates, living cells etc [42] to design new products which can help to solve housing shortage issues.
Abbreviations
AR- Augmented Reality
CD - Construction Demolition
CE- Circular Economy
CDW – Construction demolition waste
CDWM- Construction demolition waste management.
DP-TP Scheme – Development Plan and Town Planning Schemes
GOI – Government of India
IR – IR (Industry 1.0,2.0,3.0,4.0), IRs Industrial Revolutions
IoT – Internet of Things
IPCC – Intergovernmental panel for climate change
MSME – Micro small medium enterprises.
PMC – Pune Municipal Corporation
PP – Project Proponent
PCMC – Pimpri Chinchwad Municipal Corporation
PMRDA – Pune Metropolitan Regional Development Authority
RP – Regional Plan
SDG – Sustainable Development Goal/S
SCP – Sustainable consumption and Production
T/M – Tools and Machinery
TOD – Transit Oriented Development
TPS – Town Planning Schemes
UN – United Nations