Introduction
Experiments
Sample Preparation and Electrochemical Measurements of the Heat-treated Plain Carbon Steels
Examination of the Corroded Sample after Polarization Tests
Results and Discussions
Corrosion Mechanisms
Conclusions
Introduction
Steel is one of the most versatile engineering materials. Depending on the mechanical and electrochemical properties, steels are widely used in different industries such as oil and gas, railways, automobiles, transportation, and various structural purposes. Hence, steels are exposed to different kinds of environments and corrode [1, 2]. Therefore, researchers have been trying to develop modified steel with excellent mechanical and good corrosion resistance properties. Several factors such as design, process conditions, composition, and microstructures guide the corrosion behavior of steels [1, 2, 3, 4]. Among them, composition and microstructures are two critical parameters to decide the corrosion behavior of steel. Steels mainly consist of ferrite (α-Fe) and cementite (Fe3C) phase which consists of different electrode potentials since the composition of ferrite (α-Fe) and cementite is different (Fe3C) [3]. Hence, the compositional and structural difference between the ferrite (α-Fe) and cementite (Fe3C) phases mainly causes the difference in electrode potentials in aqueous solution (electrolyte) that leads to the formation of different types of micro galvanic couples and triggers the micro galvanic corrosion [5, 6, 7, 8]. In the galvanic cell corrosion, the dissolution of the more anodic (ferrite, α-Fe) phase occurs and the more passive cathodic phase (cementite, Fe3C) remains undissolved. In addition, in the galvanic cell corrosion, the dissolution behavior of anodic phases is directly influenced by the interfacial area of cathodic phases (cementite) and anodic (ferrite) phases [9, 10]. Hence, the microstructural and compositional effect on the corrosion behavior is predominantly due to the forming of the micro galvanic couples between different phases [11].
For instance, pearlite steel is a two-phase material composed of hard cementite lamellae phase embedded in a soft ferrite matrix and arranged alternately. In pearlite steel, the corrosion advances by the formation of alternate galvanic couples of ferrite and cementite plates in an aqueous solution [1, 2, 3, 4, 10, 11, 12, 13, 14, 15]. Hence, throughout the corrosion of different carbon steel, anodic dissolution of the ferrite phase occurs and leaves behind a skeleton of the hard cementite phase (Fe3C). Therefore, the fraction of pearlite finesses of the pearlite (pearlite colony size and interlamellar spacing) microstructures of steels significantly altered the corrosion behavior of steels [13, 15, 16, 17, 18, 19, 20, 21, 22, 23, 24, 25, 26]. Though the literature has also confirmed that the corrosion mechanisms of the different pearlite microstructures, as well as different carbon steels in 3.5% NaCl solution, have been broadly recognized [8, 15, 16, 17], some other aspects, such as the amount of pearlite present in different carbon steels, the effect of pearlite colony size and interlamellar spacing on the corrosion behavior, and its corrosion-related mechanisms are still not clear [1, 2].
After the extensive literature survey on the corrosion behavior of plain carbon steels, it can be concluded that the SEM and AFM topographic images have helped to understand the differential dissolution behavior of the phases as well as the extent of corrosion that occurs in the steel with the different fineness of the microstructures [1, 2, 3, 4, 5, 6, 7, 8, 9, 10]. Hence, the present investigation has been mainly dedicated to finding differential corrosion mechanisms involved in a wide range of microstructures such as ferrite, the different fraction of ferrite-pearlite, and the various fineness of pearlite steels. In this regard, SEM and AFM studies might play a crucible role to confirm the involved corrosion mechanisms. Therefore, the detailed analysis of four different variants of fully pearlite (coarse, medium, fine, and very fine) steels, as well as four different carbon (annealed 0.002%C, 0.17%C, 0.43%C, and 0.7%C) steels have been investigated and examined with the aid of AFM topography images.
Therefore, the effect of different carbon content and corresponding microstructures on the corrosion behavior of steels has been discussed with the aid of polarization tests in freely aerated 3.5% NaCl solution [27, 28, 29]. For this intention, ultralow carbon (~100% ferrite), low and medium carbon (ferrite-pearlite steels having ~ 32.74% and ~ 52.34% pearlite phase, respectively) and high carbon steels (~100% pearlite) have been used in annealed conditions to examine the effect of pearlite on the corrosion behavior of plain carbon steels. On the other hand, four different variants (coarse, medium, fine, and very fine) of pearlite steels have also been developed by suitable heat treatment (annealing, as received, normalizing, and force normalizing, respectively) process using the 0.7% carbon steels to understand the role of interlamellar spacing and pearlite colony size on corrosion mechanisms of the pearlite steels.
Experiments
Sample Preparation and Electrochemical Measurements of the Heat-treated Plain Carbon Steels
The different carbon (0.002%C, 0.17%C, 0.43%C, and 0.7%C) steels selected for the present study were obtained from the market to understand the corrosion mechanisms of the steels. Annealed microstructures of different carbon steels and different microstructures of 0.7%C steel are obtained by proper heat treatment conditions in a muffle furnace. The details of the heat treatment and further sample preparation for microstructural analysis are given in our earlier publications [1, 2, 29]. The polarization tests of all the heat-treated specimens were performed in a conventional three flat bottom cell using Parstat 2263 potentiostat (Princeton Applied Research, USA). Before polarization tests, all the steel specimens were mirror-polished. The corrosion current density (icorr) and corrosion potential (Ecorr) value for all the specimens were obtained from the Tafel extrapolation method.
Examination of the Corroded Sample after Polarization Tests
After polarization tests, the FE-SEM and AFM micrographs were used to identify the involved corrosion mechanisms of all the heat-treated steel specimens just after finished the polarization tests. This has helped to avoid the formation of any sign of corrosion products on the corroded surface. All the corroded specimens were carefully examined after cleaning with the running distilled water to identify the corrosion mechanisms and differential dissolution behavior of chemically dissimilar phases of steels. Since the FESEM images are not suitable for the calculation of the extent of the dissolution of the phases, AFM analysis was also carried out in detail to examine the corroded specimen surface to get a 3D topographical mapping. Therefore, the current study is mainly focused on the investigation of the differential dissolution behavior of the different phases of steel with varying compositions and microstructures with the aid of AFM images. All the AFM studies were carried out in the contact mode with asylum research AFM (MFP3D) at a scan rate of 0.5 Hz. The AFM probe (cantilever tip) scans the corroded specimen by keeping a constant force between the probe.
Results and Discussions
All the microstructural information and corresponding electrochemical response data obtained from the SEM micrographs and polarization curve, respectively are tabulated in Table 1[1, 2]. The ImageJ software has been used to quantify the various SEM images to obtain the interlamellar spacing and pearlite colony sizes. Since the ultra-low carbon steels contain 0.002%C, distributed form of very few precipitated carbides can be witnessed on the surface. However, any sign of pearlite is not observed on the ultra-low carbon steel specimen (as shown in Figure 1(a)).
Table 1.
Microstructural features and properties of plain carbon steels [29]
Figures 1(b) and 1(c) show the ferrite-pearlite microstructures. The fraction of pearlite content has been increased (low and medium carbon steels) as the carbon contents increased from 0.17%C to 0.43%C (as shown in Figure 1(b) and 1(c)). The average interlamellar spacing of the pearlite in annealed ferrite-pearlite steels and fully pearlite (0.17%, 0.43%, and 0.7% carbon) is measured to be 731.3±74.7 nm, 373.3±61.42 nm, and 283.48±61.17 nm, respectively.
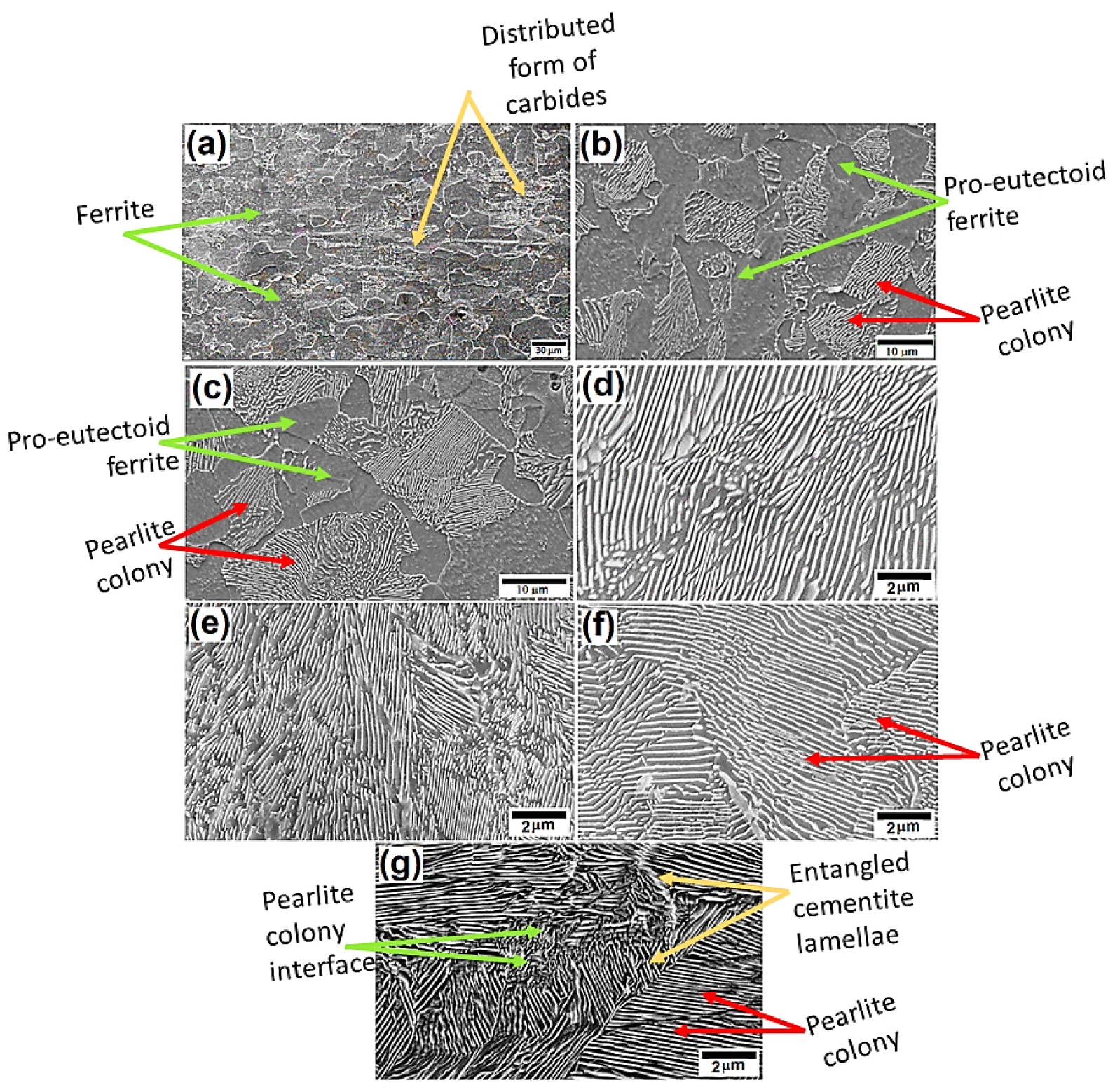
Figure 1.
SEM images of low, medium and high carbon steels containing (a) 0.002% C ferrite steel, (b) 0.17% C ferrite-pearlite steel, (c) 0.43% C ferrite-pearlite steel, (d) 0.7% C annealed pearlite steel (e) 0.7% C as received pearlite steel (f) 0.7% C air-cooled pearlite and (g) 0.7% C force air-cooled pearlite steel obtained after 3% Nital etching.
Figures 1(d-g) show the microstructures of the pearlite steels with increasing levels of fineness. The average interlamellar spacing of the pearlite is measured to be 283.48±61.17, 254.75±54.92, 236.39±33.43, and 178.66± 25.84 nm for the coarse, medium, fine, and very fine pearlite steels, respectively. Figure 1(g) shows the microstructures of the very fine fully pearlite steel. Since the cooling rate is very fast the larger cementite nucleation leads to the formation of a very small pearlite colony as well as an entangled form of cementite lamellae (shown by pair of arrowheads in Figure 1(g)). However, the entangled cementite is formed in the forced air-cooled steel due to sluggish diffusion of C and Fe atoms since the cooling rate is very high in the case of force air-cooled steel as compared to other steels. Hence, the perfect parallel plate shape formation of the cementite lamellae morphologies is not thermodynamically feasible due to very fast cooling sluggish the diffusion of C and Fe atoms. This incomplete formation of alternate cementite lamellae is named “entangled cementite” since it seems to entangle each other.
The polarization curves for all the heat-treated steel specimen is shown in Figure 2. The corrosion current density (icorr) and the corrosion potential (Ecorr) values of all the steel samples were obtained by the Tafel extrapolation method (Table 1) and obtained various other electrochemical details have been reported in our earlier publications [1, 2].
However, all the microstructural constituents and their effect on corrosion behavior are shown in Figure 3 (a-c). Figure 3(a) shows the correlation of different carbon content, the fraction of pearlite, and interlamellar spacing on the icorr and Ecorr value. This has signified that the increase in carbon content leads to a substantial change in the corrosion behavior resulting in a higher icorr value. However, a further increase of carbon (from 0.17%C to 0.43%C to 0.70%C) enhances the fraction of pearlite contents that leads to the higher icorr since the number of micro galvanic couples has also increased.
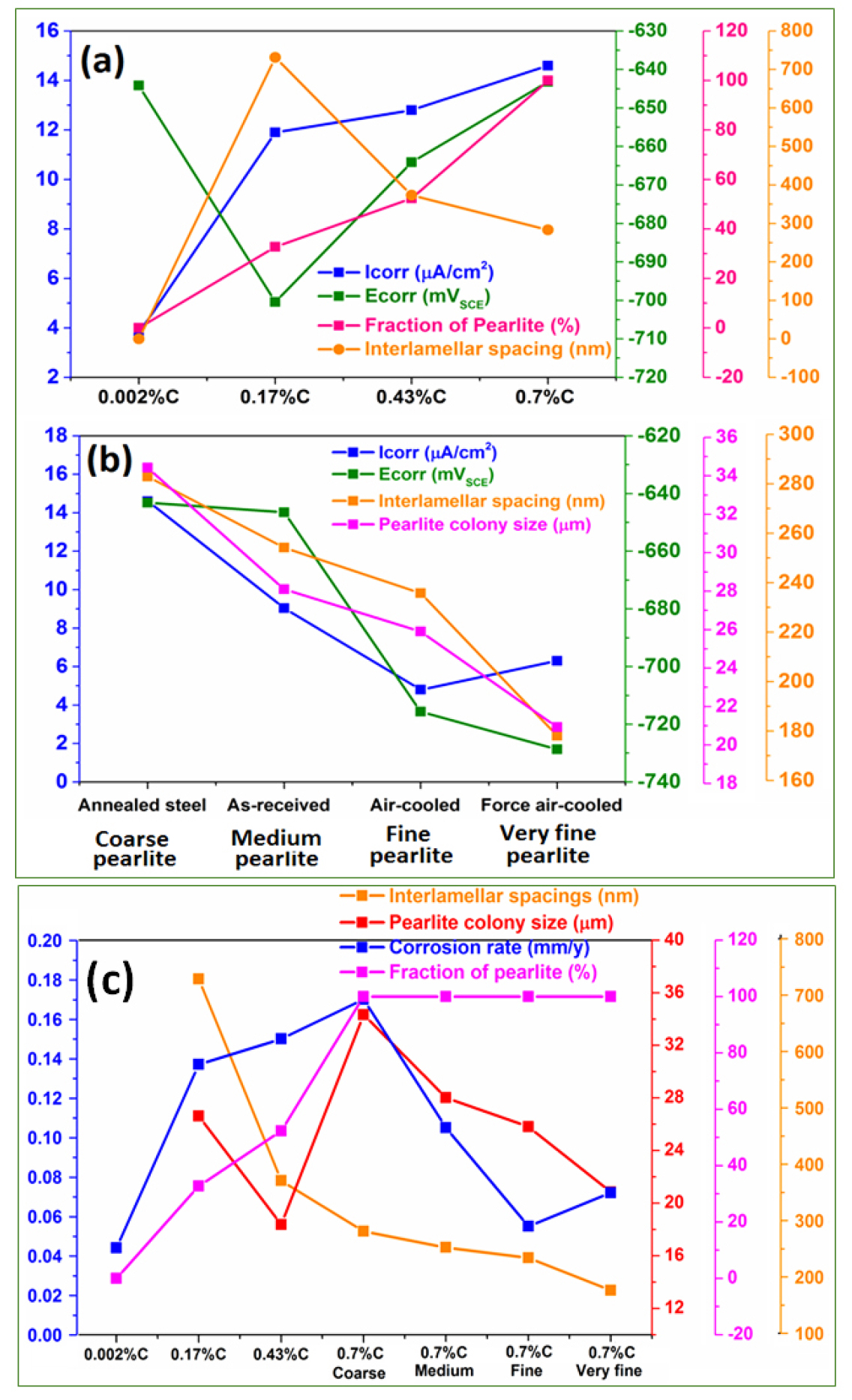
Figure 3.
(a) The correlation of the different carbon content, the fraction of pearlite, and interlamellar spacing on the corrosion current density and corrosion potential value (b) the correlation between the fineness of the pearlite microstructures on corrosion current density and corrosion potential value (c) the correlation between the pearlite colony size, fraction of pearlite, and interlamellar spacing on corrosion susceptibility.
This could be because the increased fraction of pearlite leads to higher cathodic activity resulting in higher corrosion. But, the Ecorr value was observed to be shifted in the more noble direction. Hence, it can be concluded that further increase of carbon (from 0.17%C to 0.43%C to 0.70%C) sluggish the corrosion rate since the interlamellar spacing decreases. Hence, the lower interlamellar spacing of pearlite colonies suppresses the corrosion vulnerability of annealed carbon steels.
Figure 3(b) shows the correlation between the fineness of the pearlite microstructures on the icorr and Ecorr value. It has been observed that the corrosion severity of the pearlite steel very much relies on the lower interlamellar spacing and very fine colony size which leads to the Ecorr value shifting to a more negative direction as a result of an increase in corrosion tendency [29]. However, the icorr value of air-cooled pearlite steel is lower than that of the force of air-cooled steel. This could be because the entanglement of cementite plates altered the formation of alternate galvanic couples to the distributed form of galvanic couples after corrosion which leads to the fragmentation of cementite plates.
Figure 3(c) shows the effect of carbon content, fraction of pearlite, pearlite colony size, and interlamellar spacing on the average corrosion rate. It has been observed that the corrosion rate of annealed steel (from 0.0002%C to 0.7%C) has increased because the fraction of pearlite increases (from ultra-low carbon steel to coarse pearlite). This could be because the fraction of pearlite colony contents (act as a cathode) increases the cathode surface area for galvanic cell corrosion. However, the further corrosion rate (after the fraction of pearlite reaches to be ~100%) is driven by the finesse of the pearlite steels. Therefore, it can be concluded that the corrosion behavior of fully pearlite steels governs by the combined action of pearlite colony size and the interlamellar spacing [28]. Consequently, the different fractions of pearlite contents and their interlamellar spacings led to the differential corrosion within the pearlite colony in 0.17%C, 0.43%C, and 0.70%C steels.
Corrosion Mechanisms
The differential dissolution attack of the phases and corrosion susceptibility on all the heat-treated steel specimens varied due to the overall effect of different carbon content, the fraction of pearlite, pearlite colony size, and interlamellar spacing. This may also be confirmed with the aid of AFM (Figures 6, 7, 8, 9, 10, 11, 12, 13, 14, 15, 16, 17, 18, 19, 20, 21, 22, 23, 24, 25) images. Figure 4 shows the schematic illustration of corrosion mechanisms of all the heat-treated steel specimens. This schematic illustration confirms the corroded SEM and AFM images substantially help to understand the differential dissolution attack of the phases in the steels after polarization tests.
Figure 5 shows the corroded SEM images of the low, medium, and high carbon steels obtained after polarization tests in 3.5% freely aerated solutions. Figure 5(a) shows the corroded morphology of 0.002%C steel after polarization tests. The uniform dissolution is observed throughout the sample along with localized attacks (shown by the arrowhead in Figure 5(a)). Since the 0.002%C steel contains a predominantly ferritic phase along with some extremely fine alloy carbides, that implies the localized corrosion attacks due to the formation of the local micro galvanic couples of ferrite and carbide phases.
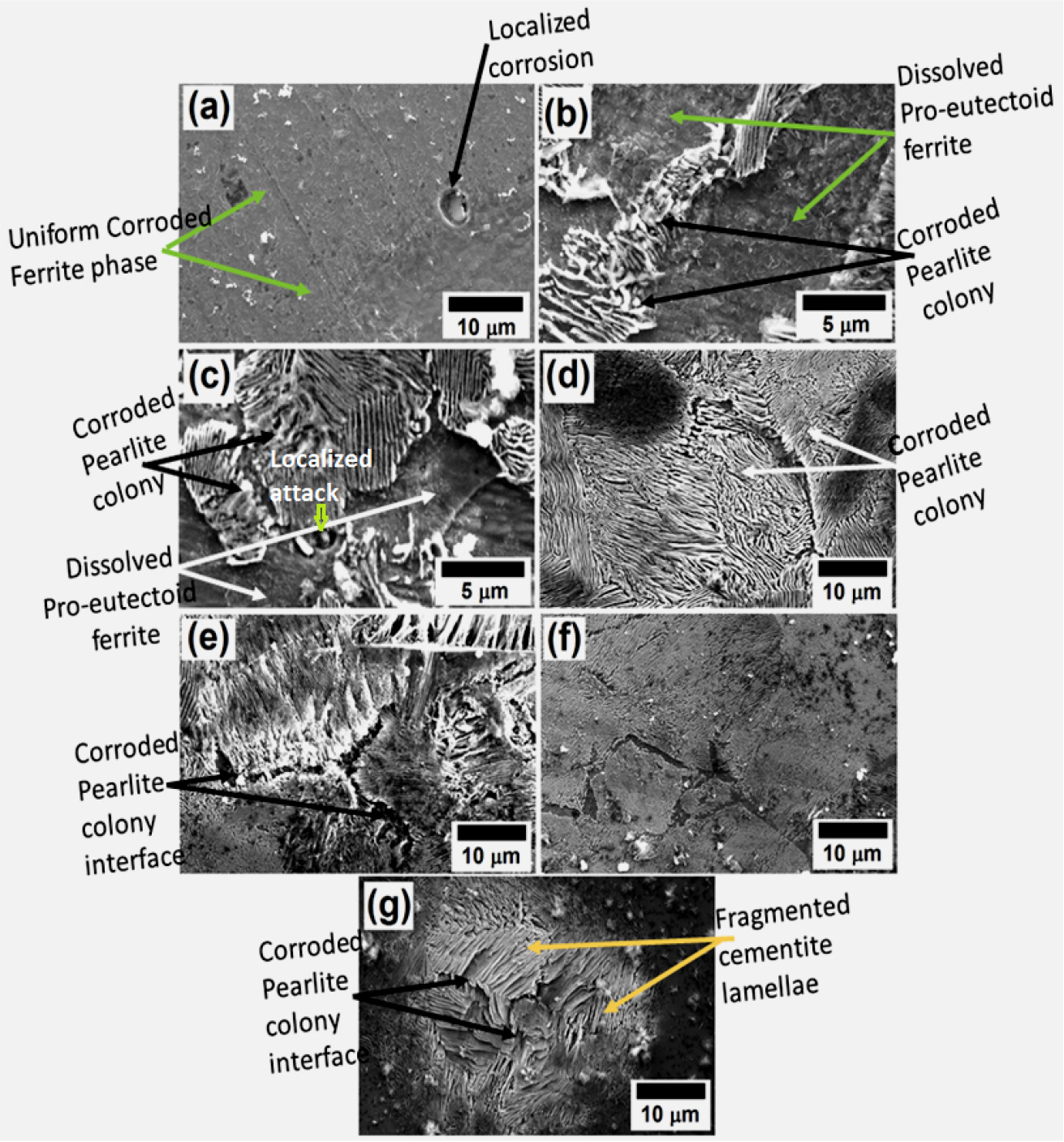
Figure 5.
Corroded SEM images of the heat-treated steel specimens containing (a) 0.002%C, ferrite steel (b) 0.17%C, ferrite-pearlite steel (c) 0.43%C, ferrite-pearlite steel (d) 0.7%C, annealed pearlite steel (e) 0.7%C, as-received pearlite steel (f) 0.7%C, air-cooled pearlite steel and (g) 0.7%C, force air-cooled pearlite steel obtained after polarization tests [1, 2].
Figure 5(b) shows the corroded morphology of 0.17%C steel containing ferrite-pearlite microstructure after polarization tests. The maximum dissolution is observed in the pro-eutectoid ferrite phase as compared to the pearlite colony since the ferrite phase is anodic to the pearlite colony. However, within the pearlite colony, intense corrosion is observed on the ferrite lamellae as compared to the cementite lamellae since ferrite lamellae are anodic to the cementite phase (Figure 5(b)). On the other hand, relatively, higher corrosion can be seen in the case of 0.43%C (Figure 5(c)) steel containing ferrite-pearlite microstructures since the higher fraction of pearlite in 0.43%C steel has increased the severity of the corrosion to a large extent. Hence, the corrosion rate has increased as well because the cathodic area increased. Therefore, micro-galvanic corrosion is highly sensitive to the area available for the cathodic reduction reaction. However, the basic corrosion mechanisms are similar to 0.17%C steel but the severity of corrosion increases due to an increase in cathodic surface area. Figure 5(d) shows the corrosion morphology of annealed 0.7%C steel containing fully pearlite microstructure. The relative intensity of corrosion is higher in the case of coarse pearlite steel since the 100% pearlite significantly increased the cathodic surface area for micro galvanic corrosion. Further corrosion behavior of coarse (Figure 5(d)), medium (Figure 5(e)), fine (Figure 5(f)), and very fine pearlite (Figure 5(g)) steel specimens depends on the finesse of the microstructure of pearlite steel. Hence, as the interlamellar spacing decreases the corrosion rate decreases except in the case of force air-cooled steel. Therefore, relatively higher corrosion can be seen in the case of coarse (furnace cooled) and medium (as-received) pearlite steel as compared to fine (air-cooled) pearlite steel. However, force air-cooled pearlite steel (Figure 5(g)) shows higher corrosion (larger dissolution in the ferrite lamellae) as compared to the air-cooled pearlite steel (Figure 5(f)) because the cementite is more entangled with each other which alter the basic corrosion mechanisms of the pearlite steel since the fragmented cementite plates significantly enhanced the cathodic reaction. The extent of dissolution and differential corrosion behavior of all the heat-treated specimens can be further understood with the aid of a 3D topographical image of AFM. Figures 6, 7, 8, 9, 10, 11, 12, 13, 14, 15, 16, 17, 18, 19, 20, 21, 22, 23, 24 show the topographic measurements of all the corroded steel specimens after polarization tests to understand the involved corrosion mechanisms.
Figure 6 shows the 3D topographic measurement of corroded 0.002%C containing ferrite microstructure steel. Distributed forms of local attack can be seen due to the presence of a cathodic nature of alloy carbides. The topography section analysis shows the extent of localized dissolution which occurred after forming the local galvanic cell corrosion. The maximum depth of dissolution at the localized region is ~0.10 um. However, the uniform corrosion of the ferrite phase is predominantly observed throughout the samples.
Typical topography measurements of pits growing (image containing –ve z-direction) in a 0.002%C steel specimen after polarization tests are shown in Figure 7. The maximum dissolution depth is measured to be ~225μm from the outer surface. The cause of the local attack was attributed to the presence of very fine alloy carbides which act as a cathodic site in the micro-galvanic corrosion. However, the rest area signifies the uniform corrosion throughout the specimen. Hence, the AFM has turned out to be an essential tool for the characterization of localized corrosion activity and the extent of dissolution of steels after polarization tests.
Figure 8 shows the AFM topography mapping of the corrosion event occurring on adjacent sites of the grain boundary as well as along the grain boundary since the grain boundary region is chemically more active as compared to the grains. Hence, the corrosion advances by the formation of micro-galvanic couples between the grains (act as a cathode) and grain boundary regions (act as an anode). The topography section analysis shows the extent of maximum dissolution (~40 nm) along the grain boundary. However, the presence of precipitated alloy carbides may also influence the dissolution behavior. This could be the reason differential corrosion has been observed at adjacent sites of the grain boundary as well as along the grain boundary in the case of 0.002%C steel.
Figure 9 shows the AFM scan image of 0.17%C steel containing ferrite-pearlite microstructures after corrosion. The image shows the movement of the tips over the corroded specimen surface for topographic measurements.
The AFM maps have shown the typical differential dissolution behavior of pro-eutectoid phase and pearlite colonies regions (as shown in Figure 10). The differential dissolution behavior of the pro-eutectoid ferrite phase and pearlite colony has occurred because of differences in the electrode potentials, however, further corrosion advances according to the fineness of the microstructures and corresponding % phase content. The topography section analysis signifies the ~ 30nm depth of dissolution of the pro-eutectoid phase since the ferrite phase is chemically more active as compared to the pearlite regions (from Figure 10). Hence, larger dissolution of the pro-eutectoid phase has occurred as compared to the pearlite colony. In addition, corrosion of the pearlite colony has also been observed.
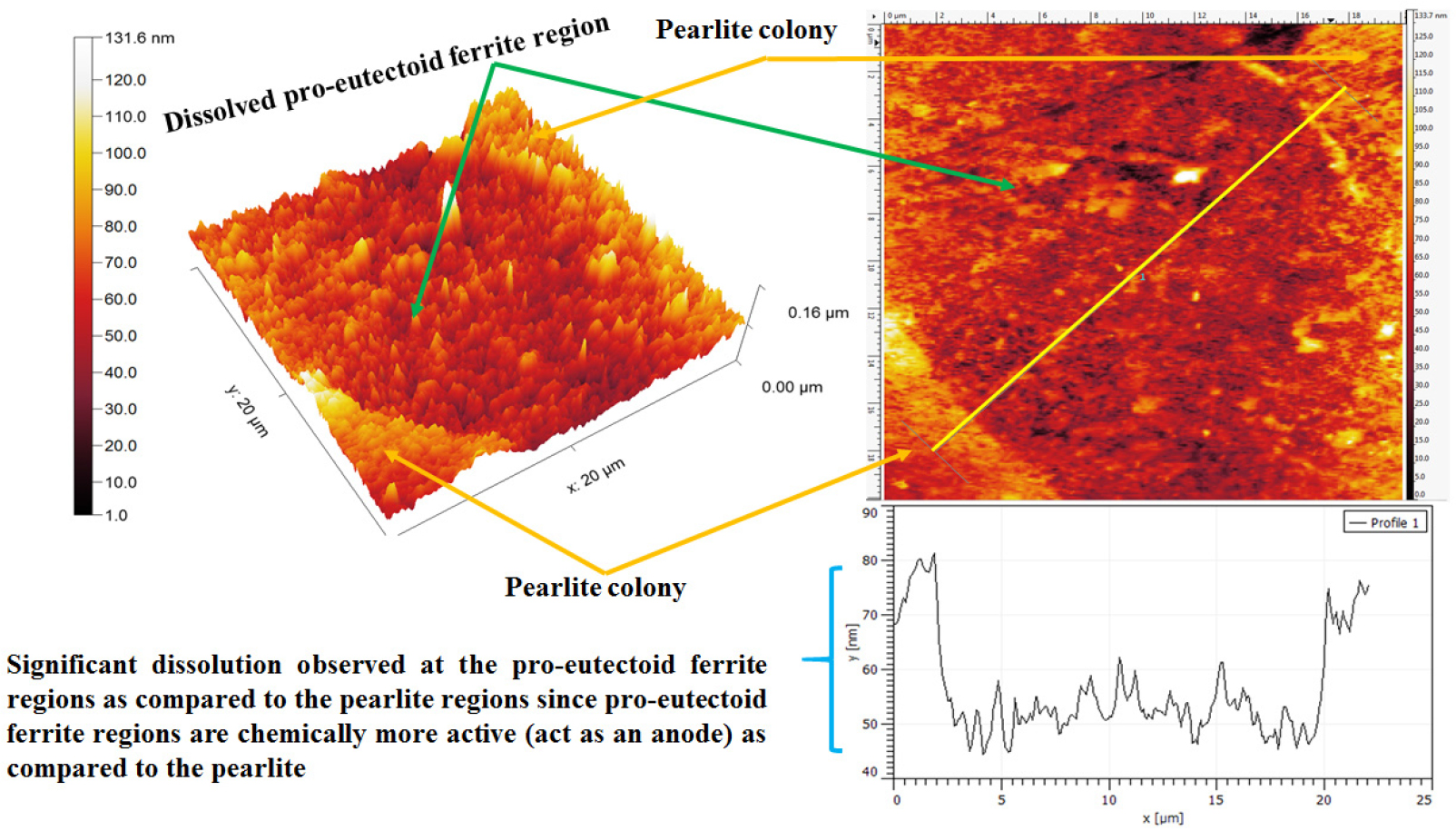
Figure 10.
The topographic AFM image of the 0.17%C steel showing the differential dissolution behavior of pro-eutectoid ferrite and pearlite colony region after polarization tests. The topography section analysis of the ferrite-pearlite steel signifies the ~ 30 nm depth of dissolution of the pro-eutectoid ferrite phase.
Figure 11 shows the differential dissolution of the pro-eutectoid ferrite phase. The dissolution of the pro-eutectoid ferrite phase has more pronounced near the side by side of the pearlite colony. Since micro galvanic corrosion is a local form of corrosion and it is limited to the contact zone. Hence, the severity of the corrosion of the pro-eutectoid ferrite phase increases rapidly as the distance from the cathode (pearlite colony) decreases (shown by two arrowheads). The topography section analysis also signifies the ~500 nm depth of dissolution adjacent to the pearlite colony. However, the depth of dissolution of the pro-eutectoid ferrite phase continuously decreases (~200 nm) away from the pearlite colony (shown in Figure 11 using curly bracket) since the cathodic activity decreases. In addition, corrosion of the pearlite colony (as shown in Figure 13, in the upcoming discussion) has also been observed since the pearlite is a mixture of alternate plates of cementite and ferrite phase.
Figure 12 shows the topographic AFM image of the corroded 0.17%C steel containing ferrite-pearlite microstructures after polarization tests. The heavy dissolution (~1μm) of the pro-eutectoid ferrite phase has been observed adjacent to the side by side of the pearlite colony (as shown in Figures 11 and 12 by a curly bracket). In addition, the local attack (~15μm) has also been observed at the pro-eutectoid ferrite phase owing to the dissolution of inclusion. However, the depth of the pitting has been measured to be ~600 nm.
However, the corrosion of the pearlite colony (as shown in Figure 13, in the upcoming discussion) has also been observed since the pearlite is a mixture of alternate plates of cementite and ferrite phase.
The differential dissolution of the ferrite and cementite plates in the pearlite colony region of the 0.17%C steel is shown in Figure 13. The depth of dissolution (~100 nm) of the ferrite and cementite plates in the pearlite colony region is due to the presence of a difference between the electrode potential of the ferrite and cementite phase causing the formation of the alternate form of micro-galvanic couples. Hence, anodic ferrite plates dissolved more as compared to the cementite plates. Katiyar et al. [29] have reported that the dissolution behavior and extent of corrosion of ferrite lamellae significantly depend upon the interlamellar spacing. As the interlamellar spacing decreases the severity of the corrosion also decreases. However, formed corrosion products after ferrite dissolution may further interrupt the corrosion susceptibility which can be depended upon the type of corrosion products formed on the specimen surface [29].
Figure 14 shows the 3D topographic AFM image of the pitting corrosion of corroded 0.17%C steel specimen after polarization tests. The severity of the dissolution of the pro-eutectoid ferrite phase adjacent to the pits is more prominent because of the electro-dissolution of anodic inclusion. The depth of the pit has been observed to the ~225 nm as shown by the topography section analysis in Figure 14. However, the size of the pits has been measured to be ~700 nm.
Figure 15 shows the dislodged cementite plates after the substantial dissolution of ferrite plates (shown by pair of arrowheads). The cementite plate also laying down since the heavy dissolution take place nearby region (~100 nm). The fragmented cementite plates have also been observed after the ferrite plate dissolution (as shown in Figure 15 by pair of arrowheads). The fragmentation of cementite plates takes place after the severe dissolution of ferrite plates. This could be the reason the dislodged cementite plates and fragmented cementite plates have been observed.
Figure 16 shows the topographic AFM image of the corroded 0.43%C steel specimen after polarization tests. The corrosion mechanisms of 0.43%C steel containing ferrite-pearlite microstructures are similar as observed in the case of 0.17%C steel specimen wherein micro-galvanic couples have formed between the pro-eutectoid ferrite and pearlite colony except for the severity of the dissolution. Since 0.43%C steel contains a higher fraction of pearlite (52.34%) as compared to the 0.17%C steel (32.74%), the severity of corrosion also increases. The topographic section analysis has shown ~140nm depth of dissolution of pro-eutectoid ferrite phase and pearlite colony (as shown in Figure 16).
Figure 17 shows the topographic AFM image of the corroded 0.43%C steel specimen after polarization tests. Intense dissolution (~600 nm) of the pro-eutectoid ferrite phase has been noticed adjacent to the pearlite colony (as shown by the curly bracket). However, the intensity of the dissolution is keep decreasing away from the pearlite colony (as observed in Figure 11). The typical localized attack has also been observed because of the presence of various constituent phases in chloride-containing environments which act as initiation sites for localized corrosion.
Figure 18 shows the AFM image of corroded ferrite-pearlite (0.43%C) steel after polarization tests. Corroded pearlite morphology of the 0.43%C steel has shown the substantial dissolution of ferrite plates causing the cementite plates to lay down one after another after the polarization tests. However, the intense dissolution of the ferrite plate also led to the fragmentation of the cementite plate (as shown in Figure 18 by pair of arrowheads). Typical corroded morphology of 0.43%C steel has also been observed in Figure 19 wherein the cementite plates tilted after the severe dissolution of ferrite plates. This could be because of differential dissolution of ferrite and cementite plates causing the cementite plate to lay down one after another.
Figure 20 shows the AFM scan image of 0.7%C (fully pearlite) steel after polarization tests wherein the tip moves over the corroded specimen surface for topographic measurements. However, all the basic parameters are the same (0.002%C, 0.17%C, and 0.43%C) for all the experiments since the extent of corrosion and differential dissolution behavior of all the specimens led to the discrepancy in the corroded 3D morphology. However, the corroded morphology of coarse, medium, fine, and very fine pearlite steel varied based on the fineness of the microstructures (as shown in Figures 21, 22, 23, 24).
Figure 21 shows the topographic AFM morphology of corroded 0.7%C steel specimen after polarization tests. Since 0.7%C steel is fully annealed coarse pearlite steel, hence dissolution behavior is mainly controlled by the interlamellar spacing and pearlite colony size. The topographic section analysis has shown ~45 nm depth of dissolution of ferrite plates (as shown in Figure 21). The severity of dissolution in each ferrite plate has also varied since the interlamellar spacing is different which directly influences the intensity of the galvanic corrosion (as shown by the curly bracket in Figure 21).
Figure 22 shows the topographic AFM morphology of corroded as-received (0.7%C) steel specimens consisting of medium pearlite microstructures. Relatively lower dissolution has been observed in the case of medium pearlite steel since this steel consists of lower interlamellar spacing as compared to the annealed (coarse) pearlite steel. The topographic section analysis has shown ~20 nm to ~37 nm depth of dissolution of ferrite plates (as shown in Figure 22) which is lower compared to the coarse pearlite steel. Hence, the dissolution behavior is mainly controlled by the interlamellar spacing and pearlite colony size. Since the interlamellar spacing is different the severity of dissolution in each ferrite plate has also varied in this case. The cementite plates morphology of the as-received pearlite steel has been observed to be different since obtained steel was cut from the rail which was the rolled product.
Figure 23 shows the relatively less corrosion (~15 nm to ~20 nm) of fine air-cooled pearlite steel as compared to coarse pearlite steel. However, in some regions, intense corrosion (~70 nm) has also been observed wherein the ferrite and cementite plates are not uniform. In this region, the non-lamellar form of micro-galvanic couples formation takes place in between the ferrite and cementite phases. Hence, distributed form of fragmented cementite has altered the intensity of the galvanic couples which leads to higher corrosion since the number of galvanic couples increases.
Figure 24 shows the topographic AFM morphology of corroded force air-cooled 0.7%C steel which consists of very fine pearlite microstructures. While comparing the corrosion behavior of the air-cooled and forced air-cooled corroded specimens, intense dissolution (~70 nm), in some regions, is observed in the case of force air-cooled pearlite steel (as shown in Figure 24 by line analysis). This could be because the physical area of the galvanic couples has increased.
In addition. entangled cementite plates were observed to be broken after corrosion which leads to the formation of more galvanic couples in between the fragmented cementite plates and ferrite lamellae. Hence, the surface area of micro-galvanic couples also increases. Consequently, a higher corrosion rate has been obtained in the case of force air-cooled steel. However, the basic corrosion mechanisms are similar as observed in the case of air-cooled, as-received, and annealed pearlite steels (as shown in Figures 21, 22, 23) except for the fineness of the microstructures (interlamellar spacing and pearlite colony size). This has largely altered the corrosion mechanisms in the case of force air-cooled steel. Therefore, relatively significant corrosion has been observed in the form of broken cementite plates (fragmented cementite) which can be seen normally after the intense dissolution of ferrite lamellae leading to the separation and fragmentation of cementite lamellae plate from the ferrite matrix.
Figure 25 shows the schematic illustration of the comparative corrosion mechanisms and dissolution behavior of coarse and very fine pearlite steel. This signifies that as the interlamellar spacing decreases the intensity of the dissolution decreases.
Therefore, the effect of the fraction of pearlite, the role of interlamellar spacing, and pearlite colony size on corrosion behavior of different carbon steels (0.002%C, 0.17%C, 0.43%C, and 0.7%C) and four different variants (coarse, medium, fine, and very fine) of 0.7%C pearlite steel under different heat treatment conditions have been discussed with the help of SEM and AFM images after the polarization tests in freely aerated 3.5% NaCl solution. The corrosion rates of the steel with different carbons follow the sequence in increasing order: ultra-low carbon steel (0.002% C) – low carbon steel (0.17% C) – medium carbon steel (0.43% C) – high carbon steel (0.7% C) since the increases in the fraction of pearlite significantly enhanced the galvanic cell corrosion results in higher corrosion rate. However, once the fraction of pearlite attains its maximum value (~100%), the corrosion susceptibility of the pearlite steel is further controlled by the finesse of the (interlamellar spacing) of the pearlite steels. Hence, air-cooled and force air-cooled pearlite steels have shown a lower corrosion rate as compared to the low (0.17%C) and medium (0.43%C) steels since the interlamellar spacing in pearlite regions is higher in the case of 0.17%C and 0.43%C steels. Therefore, the interlamellar spacing of the pearlite regions has played a crucible role to control the corrosion behavior of plain carbon steels. However, the corrosion susceptibility of high carbon pearlite steel increases in the following sequence air-cooled (fine) – forced air-cooled (very fine) – as received (medium) –annealed (coarse) steel since variations in the finesse of the pearlite microstructure significantly alter the corrosion behavior of pearlite steels. Therefore, the corrosion susceptibility of all the steel specimens has been mainly governed by the combined effect of fraction of pearlite (%), pearlite colony size, and interlamellar spacing.
Conclusions
The corrosion rates of the steel with different carbons follow the sequence in increasing order: ultra-low carbon steel (0.002% C) – low carbon steel (0.17% C) – medium carbon steel (0.43% C) – high carbon steel (0.7% C). However, the corrosion susceptibility of high carbon pearlite steel increases in the following sequence air-cooled, forced air-cooled, as received and furnace annealed steel since variations in the finesse of the pearlite microstructure significantly alter the corrosion behavior of pearlite steels. The corrosion mechanisms of all the heat-treated steels are successfully explained with the help of corroded AFM micrographs. The section analysis of AFM images helps to understand the extent of differential dissolution of steels. The topography AFM images have confirmed that the corrosion rate of all the steel specimens has been directed by the combined action of the fraction of pearlite (%), interlamellar spacing, and pearlite colony size. The topography AFM images have also helped to understand the severity of the corrosion wherein the interfacial area of the ferrite and cementite phases played an important role to decide the intensity of the dissolution.