Introduction
Material and Methodology
Definition of the investigation sample
Definition of analysis criteria and formulation of a datasheet
Data accessibility analysis
Comparative analysis
Results
Discussion
Materials and Applications
Product circularity
Energy consumption and Reduction of emissions
Workers’ safety and health
Conclusions
Introduction
Additive Manufacturing (AM) is one of the most promising and empowering technological innovations of the Industry 4.0 era due to its potential to break through the traditional manufacturing paradigm and drive the transition toward a sustainable, automatised, digitised construction Industry [1]. This innovative technological system can be considered a “design-driven” process that consents to fabricate a physical object from a three-dimensional (3D) digital model [2], offering unprecedented design flexibility [3, 4, 5]. While AM refers to the entire process, 3D printing (3DP) refers only to the production phase through printers that typically create the objects lying down and bonding many successive thin layers of materials. The advantage of AM technology is that it can be combined with robotics, modelling software, digitalisation, and the internet, creating new opportunities and progress for the efficiency of the construction sector [6, 7].
However, AM in the construction industry has fallen behind, failing to match the rapid growth it has experienced in other sectors such as healthcare, aerospace and automotive [8, 9, 10, 11, 12]. The European Construction Sector Observatory (2019) attributes this slower adoption to 1) the disruptive nature of the technology, which is still progressing through its typical innovation cycle, transitioning from early demonstrations to niche markets; 2) its limited scope of application for standardised components requiring structural reinforcement; and 3) the absence of established standards and regulations. Several factors challenge the adoption of AM processes:
-Characteristics inherent to the 3DP technology1): material selection; printability; buildability; open time2); scalability; structural integrity [4, 13, 14, 15, 16, 17, 18, 19].
-Security concerns refer to digitalisation and legal consequences, such as copyright, patents, and trademarks, with a probability of counterfeiting increase [7, 14].
-Lack of knowledge and expertise. It is crucial to develop AM knowledge so users can recalibrate their behaviours and processes to benefit from 3D printing’s capabilities. Moreover, the launch of new technology into a conventional construction sector needs to be supported by the introduction of specialised professionals able to develop new processes based on eco-efficient criteria and enhance the effectiveness of the sustainability transition [12, 13, 20].
Meanwhile, the building sector is responsible for 34% of global energy demand and 37% of carbon CO2 emissions [21]. The European Commission (2022) has estimated that the construction sector requires a significant quantity of natural resources, accounting for 50% of the total European extracting materials, and is responsible for generating 35% of the total European waste. In this context of growing awareness of the construction sector’s environmental footprint, new 3D printing technology has entered Industry 4.0 over the past decade, affecting most industrial sectors. 3D printing is showing an impressive market growth rate of 25 % [22], so product and process sustainability is crucial for the near future development of the construction manufacturing sector.
Major international treaties, including the Paris Agreement (2015) [25], have acknowledged the building sector’s pivotal role in mitigating climate change and achieving the Sustainable Development Goals.
All stakeholders within the construction ecosystem must increasingly navigate a growing array of policies and programs to foster the implementation and assurance of sustainable construction processes and building products:
-European Green Deal (2020): this set of strategic initiatives aims to achieve climate neutrality by 2050. With its adoption, the EU and its Member States are committed to reducing net greenhouse gas (GHG) emissions in the EU by at least 55% by 2030, compared to 1990.
-Directive (UE) 2024/1275 on the energy performance of buildings (recast), known as the “Green Homes Directive”. This directive is part of the broader European Green Deal. The goal is to build zero-emission buildings (ZEmB) to construct public buildings starting in 2028 and new residential buildings starting in 2030.
-The New Circular Economy Action Plan (2020) is integral to the European Green Deal. It focuses on ensuring the sustainability of building products’ life cycles even through the introduction of new technologies.
Accordingly, implementing research programs and initiatives to foster technological innovation in the construction sector, e.g. AM, with a particular emphasis on energy efficiency, sustainability, and digitisation, provides a crucial support structure for the sector’s transition under the evolving regulatory landscape at the international and European level. This objective is exemplified by several calls of the Horizon Europe program (2021-2027) [26] and the Life Program [27], focused on promoting innovative technologies to promote the energy efficiency of the building sector (e.g. Horizon Europe - Work Programme 2025, Digital, Industry and Space).
Following these research programs, academics and private companies are involved in projects (e.g., IMPRESS project3), REPAIR 3D4)) funded by the EU community that have identified the 3D printing process as a potential avenue for innovative development within the field of Additive Manufacturing. Academics and private companies are also engaged in experimentation with a diverse range of materials (e.g. innovative earthen mixtures, biological compounds, biobased polymers, etc.), applications (e.g. pavilions, installations, facade sub-components, structural elements, etc.), and printing technologies (e.g. printers on the market modified for printing innovative materials), leading to the creation of new patents.
Following a similar approach, the research project REVERSING (“Regenerative EnVelopE foR deep regeneration of School and office buildINGs”) and R3NEW (“Regenerative 3D-Printed Envelope for New Environments in Public Building Renovation”) - funded by the Regional Development Fund 2025-2030 and developed by the Architecture Department of the University of Florence - focus on innovating and developing an advanced building envelope system with high thermal and acoustic performance, including the creation of interior and exterior finishes through 3D printing techniques using innovative materials.
As part of these research activities, an initial literature review on the application of 3D printing technologies in architecture was conducted, identifying two distinct branches of use:
-Large-scale 3DP[11, 12, 14, 17, 28, 29, 30, 31], supported by large-scale machinery (gantry systems, robotic arms, multilevel large-scale printers [32] or teams of mobile robots [33], has thus far been employed for the construction of new buildings in a single piece.
-Small-scale 3DP[3, 4, 17, 34], powered by off-site printers that can fabricate a product generally with a volume smaller than one cubic meter, enables the prefabrication of modular, dry-assembled (and disassemblable) building sub-components that can be used for maintenance, renovation, and new construction, in line with the principles of circular economy [35].
Large-scale 3DP has the benefits of reducing construction time labour, increasing safety on site, and reducing waste material. However, this type of fabrication presents several issues from the perspective of the machinery employed: high cost, large size, lack of portability, and incompatibility with certain printing families and materials. Indeed, there is a significant challenge in controlling the final material properties in situ. Furthermore, the printing accuracy and quality are both poor.
On the other hand, small-scale 3DP is more accessible (in terms of cost and size) and includes various printing types. Moreover, it can be adapted to several materials, including fibre composites. It offers greater control over print quality (the possibility of printing high-complexity shapes, customised products and shapes, and tailor-made pieces) and the printing environment, improving the control over the final material performance.
Given this background, the building envelope is the focal point of the study, as Strauß & Knaack have observed:
«The building envelope is – due to functionality and industrialisation of the industry – one of the most challenging parts of the building. It has a multitude of expected performances. It separates the inside from the outside and gives the face to the building. For the one-of-a-kind architectural designs, the facade is the suitable part of building construction to represent the design intent of the customer, architect and user» [34].
Moreover, Sarakinioti et al. (2018) observe that the façade, a building’s most challenging part, exhibits a high degree of complexity in form and function. Additionally, they note a growing interest in applying advanced building envelope solutions, both in the context of research activities and industrial developments.
Accordingly, this paper will comprehensively analyse envelope subcomponents obtained through small-scale additive manufacturing processes currently available on the market or being tested within university research centres, evaluating the performance and sustainability of the 3D processes.
The Research Questions (RQ), therefore, are:
1.Which Additive Manufacturing processes are the most suitable for producing innovative, sustainable envelope sub-components?
2.Which small-scale 3D printing processes and materials should be employed?
To answer the RQs, the research activities are divided into two phases (Figure 1):
1.An analysis of 13 case studies of small-scale 3DP envelope subcomponents;
2.An evaluation and comparison of digital modelling, printing processes, materials, and performances according to sustainability qualitative parameters.
Finally, the study aims to establish a system for mapping sustainable products by surveying their sustainability performance. This will orient construction stakeholders in Additive Manufacturing and small- scale 3D printing applications, thereby increasing innovation and sustainability in envelope intervention.
Material and Methodology
The R3NEW project state-of-the-art has been carried out by analysing 13 case studies of small-scale 3D printing envelope subcomponents developed by private companies and University research groups from Europe, Asia, and America [4, 15, 36, 37, 38, 39, 40, 41, 42, 43, 44, 45, 46, 47, 48, 49, 50, 51, 52, 53, 54, 55, 56, 57, 58, 59, 60, 61, 62, 63, 64, 65, 66, 67, 68, 69, 70, 71, 72]. The analysis progresses through two consequential phases (Figure 1), as illustrated in the following paragraphs and Figure 2.
Definition of the investigation sample
The case study research was conducted by including articles published in scientific journals, handbooks, and other materials accessible from open repositories (Scopus, Web of Science, and Google Scholar), web searches (Google), and online journal articles published on sites dedicated to Additive Manufacturing and 3D printing (e.g. 3Dnatives, All3DP), as well as on the websites of 3D printer companies.
The selection criteria for the selected case studies were:
-construction products or building components realised by Additive Manufacturing processes with the potential to be used in the building sector for envelope applications;
-small-scale 3D printed façade components made with industrial printers5);
-technological systems made by University research centres, private companies, and private-public partnerships.
Building products made by artisans and artists were excluded because they were difficult to integrate into the industrial construction sector.
The chosen case studies include 13 small-scale 3D printing envelope subcomponents divided into two macro-categories: 1) innovative modular envelope sub-components and 2) bio-based6) innovative envelope sub-components.
The datasheets describes the small-scale 3D printing envelope subcomponents, which are analysed in Table 1.
Table 1.
Matrix of 13 small-scale 3D printed envelope sub-components case studies
n. | Name | Designers | Data | Location | Research category | References |
1 | Ceramic house | Studio RAP, Architecture firm | 2023 | Amsterdam, The Netherlands | Innovative and adaptive envelope modules | [36, 37, 38] |
2 | New Delft Blue | Studio RAP, Architecture firm | 2019 | Delft, The Netherlands | Innovative and adaptive envelope modules | [39] |
3 | Multi-nozzle Additive Manufacturing | T. Younger, T. Li, Q. Zheng, A. Prior. Bartlett School of Architecture, UCL | 2023 | London, UK | Innovative and adaptive envelope modules | [40, 41] |
4 | SPONG3D | Delft University of Technology, Eindhoven University of Technology and KIWI Solutions | 2017 | Delft, The Netherlands | Innovative and adaptive envelope modules | [15, 42, 43, 44] |
5 | ADAM | TU Delft, Peutz, Materialise e NWO Open Technology | 2020 | Delft, The Netherlands | Innovative and adaptive envelope modules | [1, 44, 45, 72] |
6 |
Arachne: 3D Printed Facade | Archi-Solution Workshop (ASW) | 2017 | Foshan, China | Innovative and adaptive envelope modules | [46, 47, 48] |
7 |
Beyond the Geometry Plastic 3D Printed Pavilion | Archi-Union Architects | 2021 | Nanjing, China | Innovative and adaptive envelope modules | [49, 50, 51] |
8 |
3D concrete printed facades | Neutelings Riedijk Architects, TU Eindhoven e Vertico | 2022- 2023 | Netherlands | Innovative and adaptive envelope modules | [52, 53, 54, 55] |
9 | PULSE | TU Delft, Yasar University, FMVG, Ector Hoogstad Architecten | 2017 | Delft, The Netherlands | Innovative and adaptive envelope modules | [44, 56, 72] |
10 | Aguahoja I | Neri Oxman, MIT Media LAb e Mediated Matter Group | 2019 | Cambridge, Massachussetts (USA) | Bio-based innovative modules | [57, 58, 60, 61, 62, 68] |
11 | Living soil walls | University of Virginia researchers team | 2022 | Charlottesville, Virginia (USA) | Bio-based innovative modules | [63, 64, 65] |
12 | Planter Tiles | IOUS Studio | 2023-WIP | Rotterdam, The Netherlands | Bio-based innovative modules | [66, 67] |
13 | Acoustic Diffuser Panels | Gramazio Kohler Research, ETH Zurich | 2020- 2021 | Zurich, Switzerland | Bio-based innovative modules | [68, 69, 70, 71] |
Definition of analysis criteria and formulation of a datasheet
The data analysis sheet is set up with an initial overview describing the general characteristics of the product. The design team, manufacturers, and the application site of the building subcomponent (if installed) are described. Furthermore, a comprehensive set of 19 quantitative and qualitative criteria (Table 2) [3, 19, 35, 76, 77, 78, 79, 80, 81, 82, 83, 84, 85, 86, 87, 88, 89, 90, 91, 92, 93] has been identified and classified into two macro-investigation categories:
a)Subcomponent technology data comprises the product’s technological characteristics and the materials used. The criteria for analysing technological characteristics are those standards for building envelope products. Particular attention was paid to the analysis of materials, which are an intrinsic link between the product ‘printability’, as evidenced by the literature review, and their circularity.
b)The Additive Manufacturing process encompasses three stages: 1) the design approach, 2) the 3D printing process, and 3) the post- processing stage.
Table 2.
Matrix of 19 analysis criteria
1. Subcomponent technology data | ||
Analysis Criteria (a) | Criteria description (b) | |
Technology | TRL | Analyzes the maturity level of a particular technology according to the Technology Readiness Levels (TRL) measurement system. For each case study analyzed, a TRL rating level (1 to 9) was assigned based on the project’s progress [76, 77, 78]. |
Integrability | Analyze the possibility of a construction component to be integrated with a system or vegetation [80, 81, 82] | |
Realization site | Describes where the component is manufactured [83] | |
Installation | Analyze the technological features related to the installation of components [84] | |
Material | Indicates name of material or composite [79, 85] | |
Material family | Identification of the group or “family” to which the material belongs through analysis of the characteristics and composition [79, 88] | |
Material composition | Identification of material composition [79, 85, 86] | |
Material origin | Identification of material origin, distinguishing between virgin resources (extracted directly from nature) and recycled materials (derived from the reuse of pre-existing materials) [85] | |
Material circularity potential | Analytical assessment the ability of a material to be used in a circular economy framework. It reflects the ability of materials to be cycled through processes such as reuse, recycling or composting, thereby minimizing waste and the need to extract virgin resources [35, 86] | |
Expected envelope performance | This evaluation examines the extent to which the envelope will, or potentially could, function as a subcomponent. In order to identify the performance of the envelope, analysis was conducted on a range of European standards, including the Energy Performance of Buildings Directive (EPBD) 2018 and the European Green Deal 2020, as well as relevant literature. | |
Product circularity potential | Analytical assessment the ability of a product to be used in a circular economy framework. It reflects the ability of products to be cycled through processes such as reuse, recycling or composting, thereby minimizing waste and the need to extract virgin resources [35] | |
2. Additive Manufacturing process | ||
Analysis Criteria (a) | Criteria description (b) | |
Design approach | Identification of the design approach that will ensure the product’s geometry and functional characteristics are compatible with the production process requirements and meet the required performance standards [3, 87] | |
3D Printing | Additive Printing Family | Identification of the specific family of technologies associated with the additive manufacturing processes through the analysis of the printing process [88] |
3D printing technology | Identification of the printing process [88, 92, 93] | |
Printer typology | Individuation of the printer typology [89, 90, 91, 93] | |
Material format | Identification of the format of the material used for the printing process [92] | |
Product dimension | Indication of finished product dimensions (related to the size of the printer) [92] | |
Printing time | Indication of the printing time required to obtain the finished product or test sample [92] | |
Post-processing | Analysis and identification of product finishing operations that may be required to obtain the finished, ready-to-use part at the end of the printing process [19] |
The criteria selected for the analysis refer to standard features of 3D-printed prefabricated envelope technologies identified through literature review or indicated by international standards for achieving the required envelope standards (e.g., UNI EN 13830 (2020) [94] on structural Integrity and Safety or ISO 14040 (2006) [95], which focuses on sustainability and environmental impact). Hence, they are not dependent on specific organisations and business strategies adopted by manufacturers.
A synthetic datasheet template was developed to streamline data systematisation. Figure 3a, 3b and 3c illustrates the sheet’s structure, which organises information into two sections based on the criteria categories under analysis. The first section focuses on subcomponent technology data, while the second addresses additive manufacturing processes.
The data collection and archiving process entailed gathering quantitative and qualitative data through literature searches. These searches encompassed articles published in scientific journals, handbooks, and other accessible materials from open repositories (Scopus, Web of Science, and Google Scholar). The references for each case study were collected within the corresponding fact sheets. Additionally, the information obtained through the literature search was complemented by the author’s direct experience, who acquired further details through professional interactions with companies and research centres, thus ensuring the comprehensive investigation of the subject matter.
Data accessibility analysis
The case study analysis highlighted a significant gap in the availability of specific data based on the established criteria. This data deficiency emerged as a crucial finding, revealing areas within the manufacturing processes that are still evolving. Public and private research teams are currently focusing on these areas to enhance the efficiency of 3D printing production for its transition into the construction industry sector.
To address these data accessibility challenges, the available and inferred data must be systematically analysed and summarised in Figure 4 as follows: a) unavailable data (empty field), b) inferred data (marked by ‘-’) and c) easily accessible data (denoted by ‘•’).
The analysis shows that:
1)Challenges in Data Accessibility at Early TRLs (1-4). Early-stage innovations tend to have limited public data due to ongoing research validation, proprietary developments, or incomplete datasets.
2)Sensitive Data Points. Innovation, whether led by private companies, research institutions, or public-private partnerships, often involves handling sensitive data. The most sensitive areas concern the research’s TRL, printing technology, printing time, and post-processing operations, which are crucial in developing market-ready products. Data collection was more difficult for these specific areas, highlighting the particular areas of research and development that organisations actively target to improve the scalability and innovation potential of 3D-printed building components.
3)Data Quality and Source Reliability. A noticeable distinction in data quality emerged between academic and industry sources. University research projects tend to produce more comprehensive, precise datasets, often enriched with methodological details and contextual references. This reflects rigorous academic research standards that prioritise transparency and replicability. In contrast, industry-led initiatives, driven by commercial interests and intellectual property concerns, often limit the scope of publicly available data.
Comparative analysis
A comparative analysis was conducted on the 13 small-scale 3D-printed envelope subcomponents. The case studies were evaluated based on qualitative parameters that examined the sustainability of the building subcomponents as industrial products and the entire manufacturing process involved in their production.
The parameters mentioned above were selected based on the investigated objects’ dual classification, defined as 1) prefabricated building products and 2) products manufactured using non-traditional processes, specifically AM technologies.
The final set of sustainability parameters emerged from a review of the existing literature on the sustainability of prefabrication technologies and products and the sustainability of processes and products created using AM. The parameters related to prefabrication were contextualised to the specific topic of 3D-printed envelope subcomponents, considering that 3D printing is, per se, a technology that was introduced to the construction sector to improve the sustainability of its resources through a waste- and formwork-free process [96], as well as optimising the cost-effectiveness of the manufacturing process.
The evaluation revealed 24 sustainability parameters organised into a matrix illustrated on Table 3[5, 35, 51, 83, 97, 98, 99, 100, 101, 102, 103, 104, 105, 106, 107, 108, 109, 110, 111, 112, 113] according to environmental, economic, and social sustainability goals [107, 114]. The fulfilment of these criteria was evaluated by analysing the data collected for each case study. Subsequently, a summary assessment matrix was developed (Figure 5) to summarise the research results presented in Paragraph 3 of the paper.
Table 3.
Matrix of 24 Sustainable Parameters
Sustainability Goals | Sustainability Parameters (SP) | |
Environment | Material circularity | The material can be reintegrated into production processes without downgrading [97] |
Low-carbon embedded materials, such as bio-based or recycled materials, are used to saving energy, reducing cost, and decreasing CO2 emissions [98, 99] | ||
Product circularity | The façade component is easily removable and replaceable, improving the maintainability of the envelope system [35, 100] | |
The product can be easily reused or recycled because it is designed to be disassembled or composed of readily disassembled sub-components at the end of its life cycle [35, 98, 100] | ||
Durability of components under expected environmental conditions to avoid frequent replacements, thus reducing energy loss and resource consumption over time [51, 99, 107, 108] | ||
Biomimetic Inspiration | Use of bio-inspired solutions [101, 102, 103] | |
The component can establish relationships with the surrounding environment and its life forms [101, 103, 104] | ||
Product-process predictability | Possibility to control the quality of the final product and the entire process by reducing errors in the early stages of the manufacturing process through the use of simulation technologies [5, 105, 106] | |
Possibility to control the quality of the final product and the entire process by reducing errors in the early stages of the manufacturing process through the use of simulation technologies [5, 105, 106] | ||
Energy consumption | The energy consumption of 3D printers is optimised by improving their efficiency and using renewable energy sources for printing operation [109] | |
The design is optimized to reduce printing time and, thus, energy and material consumption during printing operations. Optimisation must consider the printing method, layer thickness and shape, and the need for support structures [110] | ||
Life cycle analysis (LCA) has been carried out [110] | ||
The post-processing phase has been optimised to reduce energy consumption [110] | ||
Reduction of emissions | Low energy demand and CO2 emissions from manufacturing processing [83, 99] | |
Material supplied from sustainably managed sources [83, 99] | ||
Material availability on the market [83, 99] | ||
Source materials locally to minimize transportation emissions and foster regional economies [83] | ||
Economy | Speed of construction | Reduction of component realization time compared to traditional manufacture [106] |
Optimisation of shape, angles and number of layers (thickness) to reduce 3D printing time [111] | ||
Ease of construction | Envelope components can be easily handled and installed by workers without using heavy-lifting equipment [83] | |
Stocking and installation of envelope components do not require specific site protection measures against weather [83, 107] | ||
Economy of construction | Envelope components are optimized for transport [83] | |
Society | Work safety and health | Manufacture processing requires minimum interaction with workers (limited to machine setting and control) [106] |
Workers are not exposed to the emission of volatile organic compounds (VOCs) and ultrafine particles (UFPs) during the printing process [112, 113] |
A sustainability mapping system was formulated through the analyses of Phases 1 and 2 (Figure 1) findings and the comparative evaluation of the case studies responding to Analysis Criteria and Sustainable Parameters. This system encompasses the strategies demonstrated to enhance the sustainability of manufacturing products and processes.
Regarding the results shown in Figure 5, the non-filling of a specific box does not necessarily imply the case study’s non-compliance with the corresponding sustainability parameter. Instead, in many cases, it reflects the lack of data related to that specific parameter, as explained in Paragraph 2.3 and Figure 4 of this article.
Results
The first phase of the research project was finalised, and 13 case study analysis sheets, structured according to 19 analysis criteria (Table 2), were collected to define the state of the art of innovative sub-component envelope solutions realised through additive manufacturing processes.
In the second phase of the research, a qualitative evaluation and comparison of each case study’s sustainability performance was conducted according to 24 qualitative Sustainable Parameters (SP), addressing three sustainability goals: a) environmental, b) economic, and c) social sustainability (Figure 4).
The following section presents the main results of Phase 2, “Evaluation and Comparison”, concerning the specific Sustainability Parameters (SP):
a) Environmental Sustainability
1.Material Circularity
-SP.01_The material can be reintegrated into production processes without downgrading [97]
-SP.02_Low-carbon embedded materials, such as bio-based or recycled materials, are used to save energy, reduce cost, and decrease CO2 emissions [98, 99]
The case studies (CS) associated with the “bio-based innovative modules” group (CS.10; CS.11; CS.12; CS.13) demonstrate the most optimal circularity characteristics for the Material Circularity goal. In particular, the case of CS.10 is composed of biological compounds (including cellulose, chitin, and pectin), offering versatility in its production and recycling at the end of its life cycle (Figure 6). Accordingly, this sub- component is fully biodegradable and designed to experience programmed decomposition when exposed to specific climatic conditions and weathering, as determined through computational modelling [59, 115].
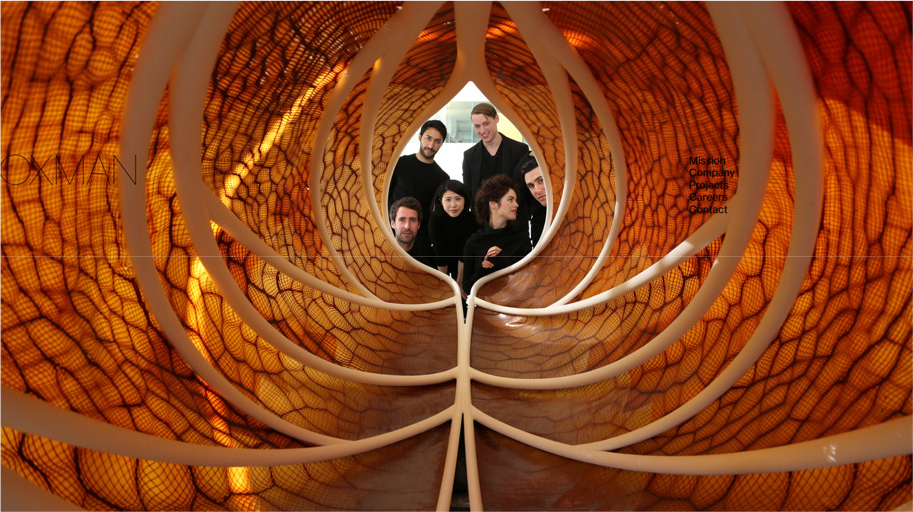
Figure 6.
Case study Aguahoja I (CS.10). Interior view of the architectural pavilion made of biological compounds (including cellulose, chitin and pectin) of different densities (Source: OXMAN practice website, [62]).
Moreover, products manufactured from clay (CS.01, CS.02, CS.12) are based on raw materials extracted directly from the natural environment and require no further treatment. These products have low emissions and high material and process efficiency. Clay can be recycled and reused indefinitely without losing mechanical properties unless it has undergone firing/vitrification processes [116] (Figure 7, 8).
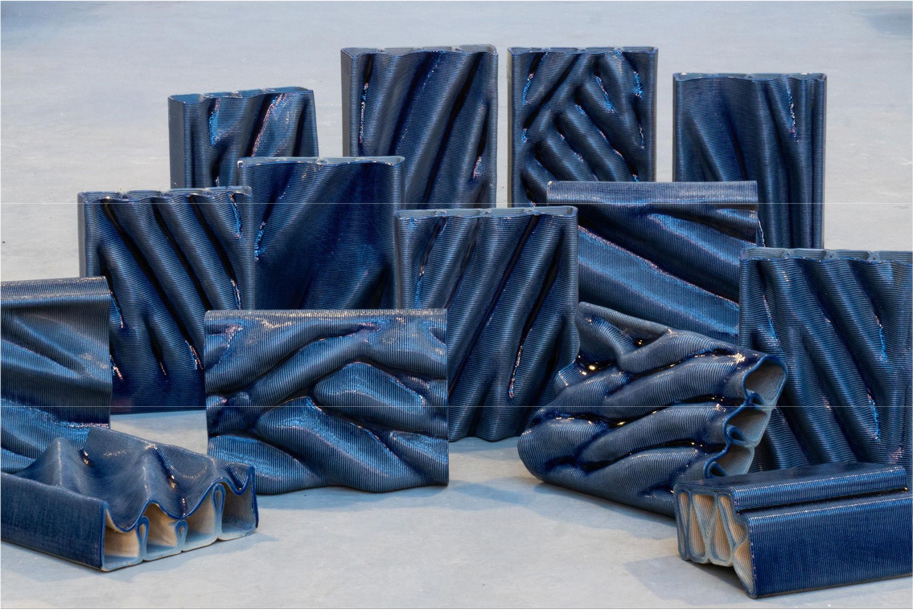
Figure 7.
Case study Blue Delft (CS.02). Types of finished tiles used for the PoortMeesters housing archway (Source: Studio RAP, [39]).
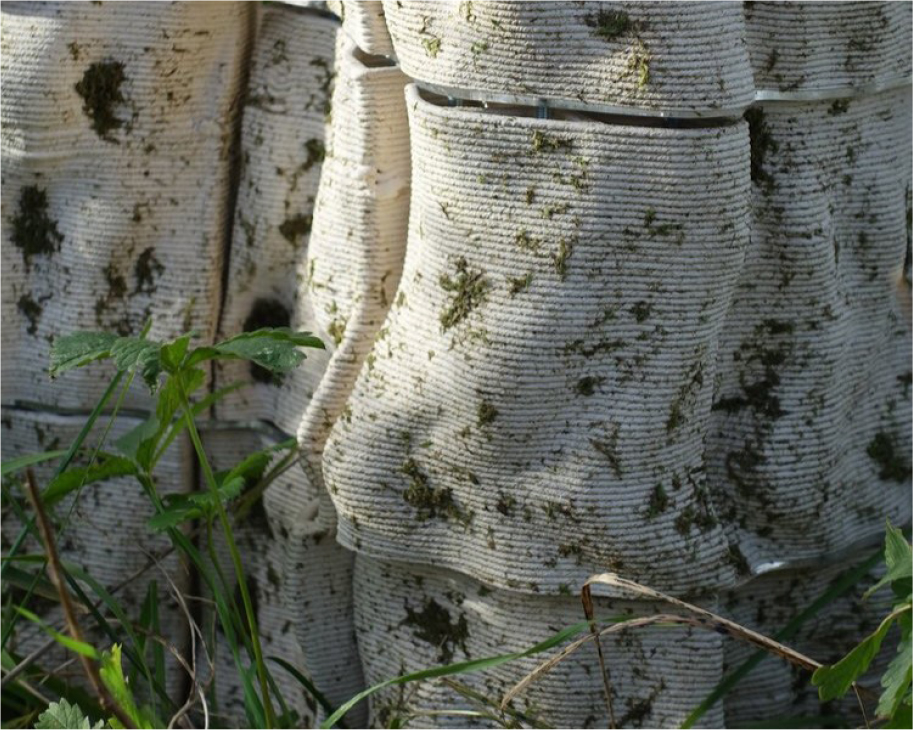
Figure 8.
Case study Planter Tiles (CS.12). Prototype of the 3D-printed moss tiles fitted together to simulate a wall (Source: IOUS Studio, [66]).
Also, the innovative modular envelope sub-components defined in CS.04, CS.05, CS.06, CS.07, and CS.09 are characterised by being composed of plastics (Acrylonitrile-Butadiene-Styrene (ABS), Polyamide 12 (PA12), Polyvinylidene Fluoride (PVDF), Polyethylene Terephthalate Glycol (PETG)). Although not manufactured from bio-plastics, such as CS.13, the analysis findings indicate they possess significant circular potential. This is due to their ability to undergo complete recycling and reuse, or reprinting, on numerous cycles. However, the material undergoes progressive downgrading [117].
CS.05 represents a unique case study. It is realised by employing PA12, printed via Selective Laser Sintering (SLS) instead of Fused Deposition Modelling (FDM). In this context, the powder used in the SLS printing process can also be recycled during the printing process itself. However, as highlighted by Machotová et al. (2024) [118], recycled PA12 does not retain its original physical and mechanical properties despite the ability to recycle and reprint this material.
2.Product Circularity
-SP.03_The façade component is easily removable and replaceable, improving the maintainability of the envelope system [35, 100]
-SP.04_The product can be easily reused or recycled because it is designed to be disassembled or composed of readily disassembled sub-components at the end of its life cycle [35, 98, 100]
-SP.05_Durability of components under expected environmental conditions to avoid frequent replacements, thus reducing energy loss and resource consumption over time [51, 99, 107, 108]
The achievement of the Product Circularity goal depends on various product characteristics, including the type of installation (dry or wet), modularity, and materials (type, origin, composition).
The case studies involving dry installation technologies CS.02, CS.03, CS.05, CS.06, CS.07, CS.09, CS.10, CS.11, CS.12, and CS.13 demonstrate more significant potential for product circularity than those using wet installation methods (e.g. CS.01, CS.04, CS.08). This is due to the ease of disassembling and dismantling the envelope system, which facilitates maintenance and replacement of both the façade and its subcomponents (Figure 9, 10, 11).
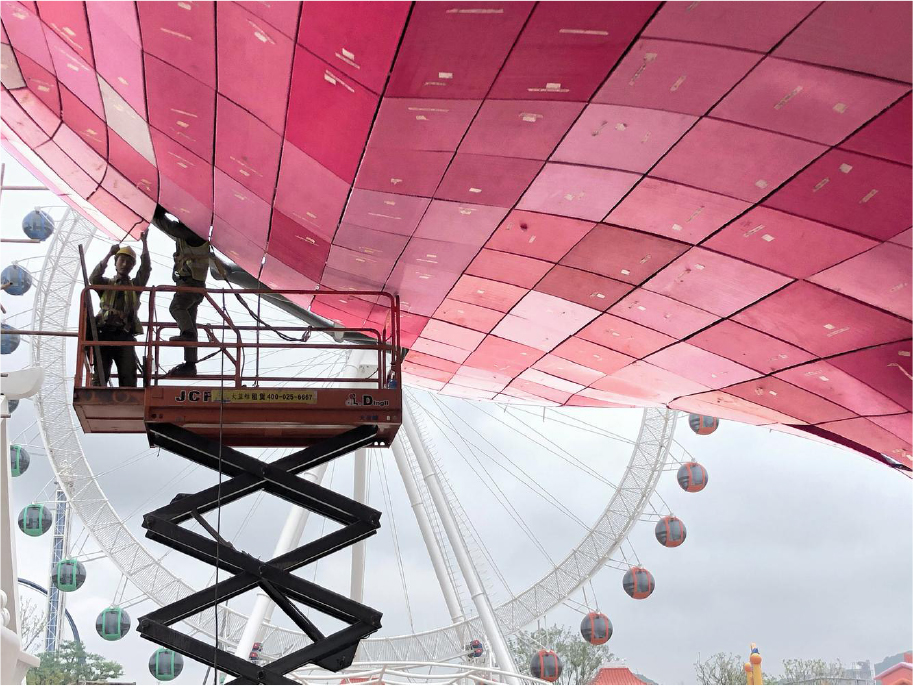
Figure 9.
Case study Beyond the Geometry Plastic 3D Printed Pavilion (CS.07). View of the dry assembly phase of the pink plastic panels to the metal substructure (Source: Archi-Union Architects, [50]).
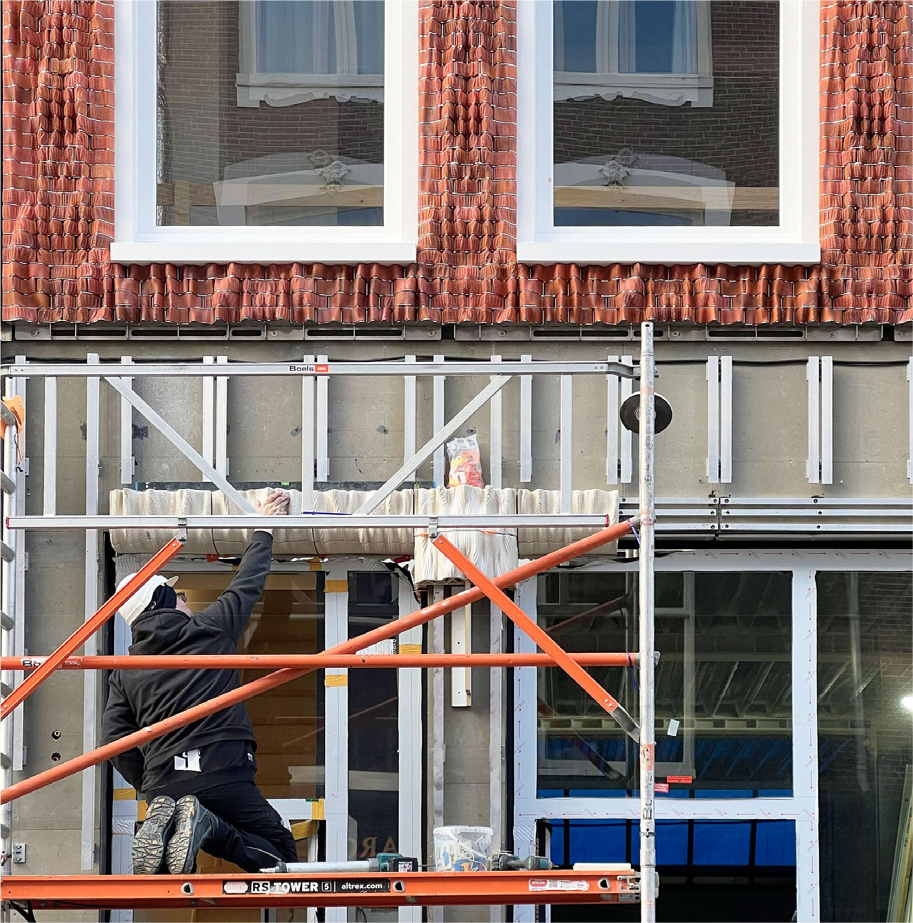
Figure 10.
Case study Ceramic House (CS.01). Dry assembly of the ceramic finish (Studio RAP, photograph by Riccardo De Vecchi, [38]).
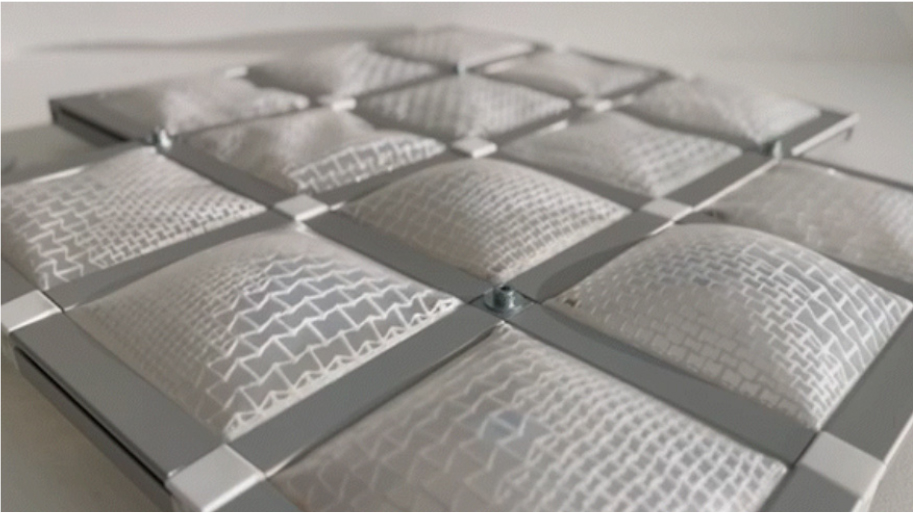
Figure 11.
Case study Multi-nozzle Additive Manufacturing (CS.03). Video frame of the functioning of the facade prototype consisting of silicone auxetic tiles (Source: WASP, [5]).
However, while dry-installed products exhibit high maintainability and recyclability, they face limitations in intermediate cycles such as reuse, redistribution, refurbishing, and remanufacturing. This limitation arises from the tailored, ‘form-fitting’ design and high degree of customisation inherent to AM processes, distinguishing them from traditional manufacturing methods. These bespoke qualities make reintegration into broader reuse cycles challenging, as the components are specifically designed for the architectural context in which they were initially implemented.
Given that customisation is a fundamental feature of 3D-printed products across all analysed case studies, parameters such as maintainability (SP.03), disassemblability, and durability (SP.05) remain crucial for ensuring product circularity. Case studies CS.10, CS.11, and CS.12 exhibit material characteristics that make them particularly suitable for controlled environments, such as the interior surfaces of building envelopes in indoor spaces, where environmental factors are more stable and predictable (Figure 12).
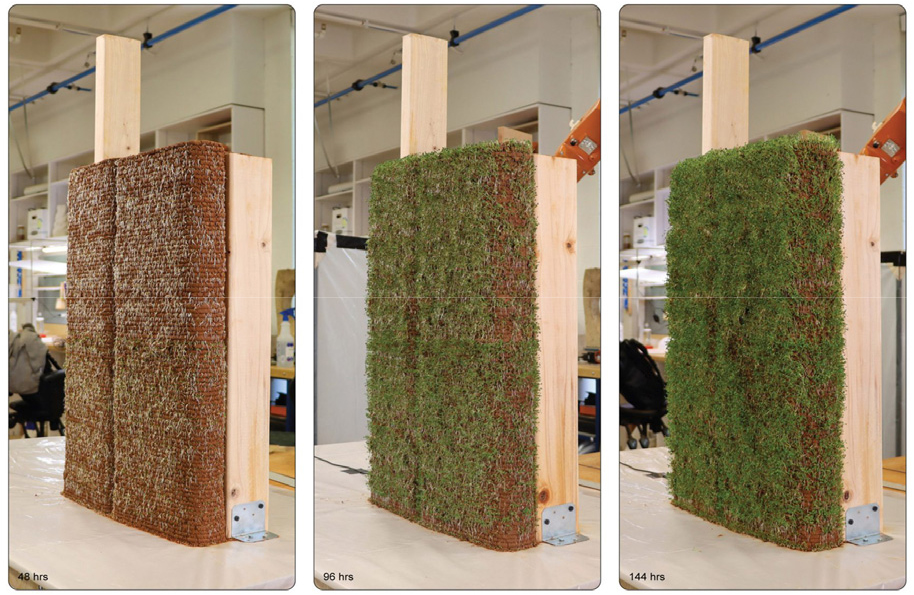
Figure 12.
Case study Living soil walls (CS.11). Germination stages of Living Soil Wall at 48, 96, 144 hours after printing (Source: DeZeen, [64]).
3.Biomimetic Inspiration
-SP.06_Use of bio-inspired solutions [101, 102, 103]
-SP.07_The component can establish relationships with the surrounding environment and its life forms [101, 103, 104]
Bioinspired design is an approach that incorporates biological principles to enhance sustainability in building envelopes by fostering a dynamic interaction with the environment. According to Ortega del Rosario et al. (2023), buildings that can respond dynamically to environmental stimuli have the potential to reduce energy consumption and mitigate environmental impacts significantly.
This biomimetic design philosophy emphasises the creation of sustainable, adaptable structures by integrating solutions inspired by natural processes and ecosystems.
Functional bio-inspiration can be applied through two distinct methods:
1) The direct approach involves closely mimicking or replicating specific natural functions observed in biological systems, aiming to translate them into architectural solutions [81]. In this context, CS.03 employs the mechanism of phototropism, observed in plants and characterised by their reaction to light, to activate kinetic systems. The design employs 3D-printed auxetic silicon membranes that undergo swelling in response to changes in light intensity, thereby enhancing energy efficiency and passive environmental regulation.
2) The indirect approach is based on a selected biological principle but requires an intermediate abstraction step to move from the biological principle to the building envelope technology [81, 119].
CS.10 demonstrates environmental reactivity by utilising temperature and humidity fluctuations. These fluctuations induce controlled structural and visual transformations, enabling this component to degrade and deform in an adaptive and controlled manner [58].
The case studies CS.11 and CS.12 exemplify the most immediate interaction with environmental ecosystems, whereby vegetation and moss species are integrated into the surface design. This design enhances biodiversity and contributes to ecosystem services, including carbon storage, CO2 absorption, heavy metal filtration, and particulate matter capture. Furthermore, these cases illustrate the potential benefits for pollinator habitats and outdoor air quality, contributing to improved thermal comfort in urban environments. Such innovations reflect a holistic approach to sustainability, extending beyond energy and resource efficiency to encompass ecological enhancement and biodiversity promotion.
4.Product-process predictability
-SP.08_Possibility to control the quality of the final product and the entire production phase by reducing errors in the early stages of the manufacturing process through the use of simulation technologies [5, 105, 106]
-SP.09_Possibility to control the envelope construction process (times and costs certainty) [83]
The case studies collectively illustrate the efficacy of the design-driven methodology in producing prefabricated envelope components, thereby ensuring superior final product quality and comprehensive control over the manufacturing process. The design-driven approach, utilising computational methods in conjunction with the component’s prefabricability, represents a significant advancement in the final control of the realisation of the envelope component (e.g. modular prefabricated façade system) (Figure 13). Even in cases involving the development of building products still in the design and testing phase (TRL 4-6), this project approach provides the potential for the future strategic management of the sub-components’ systemic application.
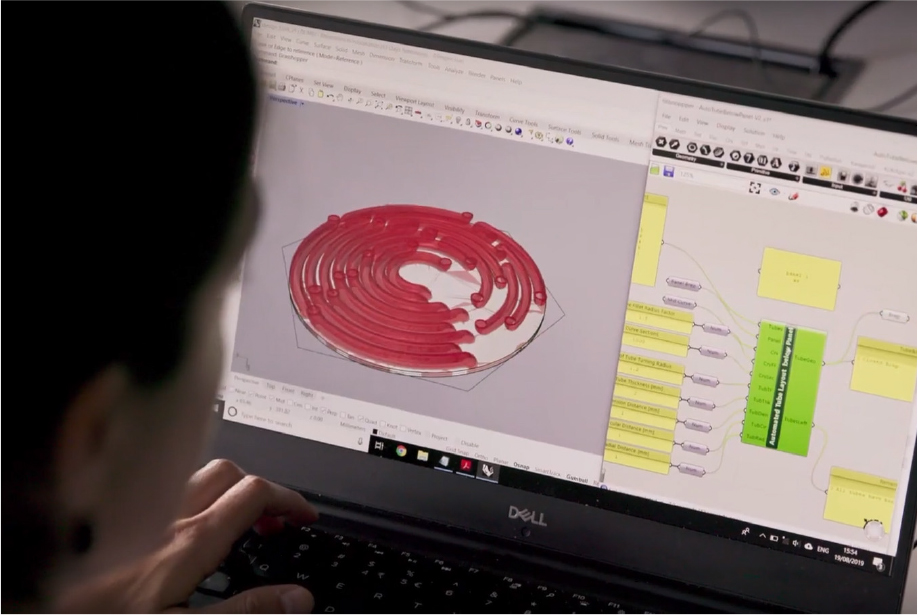
Figure 13.
Case study ADAM - Acoustics by parametric Design and Additive Manufacturing. The product design phase uses computational design models and associated software such as Rhinoceros and Grasshopper (Source: video frame of the project presentation made by the research team, [72]).
5.Energy consumption
-SP.10_The energy consumption of 3D printers is optimised by improving their efficiency and using renewable energy sources for printing operations [109]
-SP.11_The design is optimised to reduce printing time and, thus, energy and material consumption during printing operations. Optimisation must consider the printing method, layer thickness and shape, and the need for support structures [110]
-SP.12_Life Cycle Assessment analysis (LCA) has been carried out [110]
-SP.13_The post-processing phase has been optimised to reduce energy consumption [110]
The analysis of the case studies concerning the sustainability parameters of the Energy Consumption Sustainability goal (SP.10, SP.11, SP.12, SP.13) yielded a significant result, clearly visible in Figure 5. Although the case studies CS.04, CS.05, and CS.09 have been developed considering the product design optimisation process about the printing process (SP.11) accurately, for none of these case studies was LCA analysis performed. Furthermore, no specific reference has been made to the use of compensation solutions or actions to reduce the energy consumption of the manufacturing process.
6.Reduction of emissions
-SP.14_Low energy demand and CO2 emissions from manufacturing processing [83, 99]
-SP.15_Material supplied from sustainably managed sources [83, 99]
-SP.16_Material availability on the market [83, 99]
-SP.17_Source materials locally to minimise transportation emissions and foster regional economies [83]
All the sub-components analysed, except for CS.10, use materials readily available on the industry construction market and directly printable without requiring additional processing. However, the state- of-the-art study shows some gaps regarding the production chain and traceability of the materials used to realise the facade components, such as the absence of references to certifications attesting to the origin and sustainable management of resources. As indicated in the section on Energy Consumption, an LCA analysis of the product was not carried out in any of the case studies, highlighting a significant area for improvement in the overall environmental impact analysis of the analysed 3D printed components.
b) Economic Sustainability
-SP.18_Reduction of component realisation time compared to traditional manufacture [106]
-SP.19_Optimisation of shape, angles and number of layers (thickness) to reduce 3D printing time [111]
-SP.20_Envelope components can be easily handled and installed by workers without using heavy-lifting equipment [83]
-SP.21_Stocking and installation of facade components do not require specific site protection measures against weather [83, 107]
-SP.22_Envelope components are optimised for transport [83]
As demonstrated by the literature review findings in Section 1, the Small-scale 3D Printing approach allows the production of small, modular and dry-assembled prefabricated components with the possibility of disassembly. When integrated into the broader context of the design-driven manufacturing process, this approach ensures precise control over the shape, weight and installation method of building components, optimising efficiency during all phases of the building envelope system, including transport, site management, installation and commissioning. This results in more efficient time, cost and safety management at each stage of the project life cycle (SP.20, SP.22).
All the case studies demonstrate that the file-to- factory approach, when combined with the use of 3D printing technologies through the use of multi-axis printers and robots, not only considerably reduces the time required in the production chain (SP.18) but also enables the design and production of high-performance components characterised by unique and customisable designs (Figure 14). The components are manufactured using innovative materials, including advanced and biological materials, which are challenging, if not impossible, to produce using conventional industrial processes (Figure 15). Nevertheless, the geometric and morphological complexity of the elements, in conjunction with the difficulties associated with the materials used, currently precludes the large-scale application of this technological approach, as it is economically inaccessible to the majority.
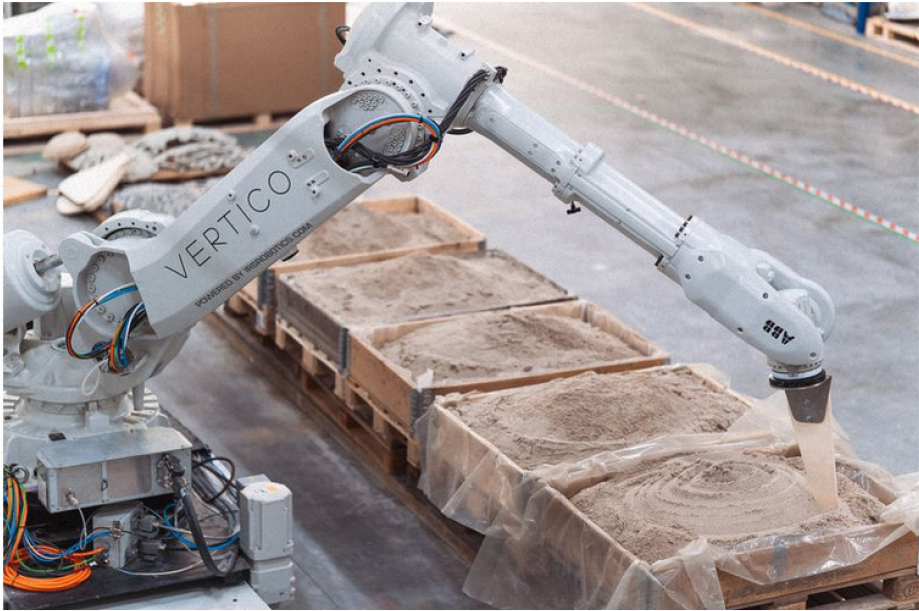
Figure 14.
Case study 3D concrete printed facades (CS.09). Sand shape modelling is fully mechanised using multi-axis VERTICO robots (Source: VERTICO, [55]).
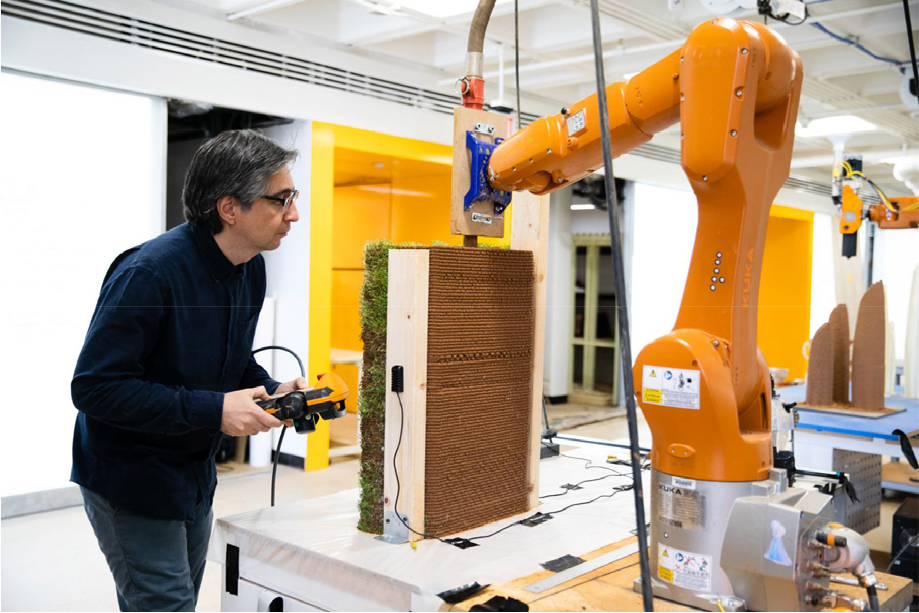
Figure 15.
Case study Living Soil walls (CS.11). Sub- component control phase by researchers with the assistance of multi-axis robots (Source: DeZeen, [64]).
In the case studies CS.04, CS.05 and CS.09, the researchers provide a detailed analysis of the efforts made in the research and prototyping phase to reduce production time and comply with the economic logic of industrial construction production while maintaining high standards of quality and functionality of the innovative product (SP.19). A comparative analysis of these case studies, the only ones to provide data on printing times and their optimisation, reveals that the utilisation of Selective Laser Sintering (SLS) facilitates superior control over printing precision and, consequently, over the quality of the final manufactured product (CS.05).
Ultimately, the case studies reveal that the “innovative bio-based modules” case study group (CS.10, CS.11, CS.12) necessitate particular protective measures during transport, storage, and installation to prevent damage caused by atmospheric events (SP.21) and ensure that the environmental conditions designed for their proper storage (CS.10) are maintained. The current use of these components is predominantly within indoor environments, necessitating regular maintenance procedures, such as periodic visual inspections, monitoring of indoor microclimatic conditions, and watering.
c) Society Sustainability
-SP.23_Manufacture processing requires minimum interaction with workers (limited to machine setting and control) [106]
-SP.24_Workers are not exposed to the emission of volatile organic compounds (VOCs) and ultrafine particles (UFPs) during the printing process [112, 113]
The analysis of case studies demonstrates that additive manufacturing processes for small-scale 3D printing rely on automated print machinery and robotic systems. These processes can enable the prefabrication of building components with minimal manual worker intervention (SP.23). Furthermore, they significantly enhance workplace safety by reducing physical strain, such as that associated with handling heavy loads, and ensuring that operations are conducted in controlled environments.
However, recent studies by Chýlek et al. (2021) and Garcia-Gonzalez et al. (2024) have highlighted potential concerns regarding air quality due to the emission of volatile organic compounds (VOCs) and ultrafine particles (UFPs) during the 3D printing phase, particularly with widely used materials such as Polylactide (PLA), ABS, PETG, and Thermoplastic Polyurethane (TPU) in the FDM printing process (SP.24). These emissions include compounds such as alkanes, benzenes, and aldehydes, with emission profiles varying according to the specific filament type and brand in question that can be dangerous to the health of operators, particularly in non-industrial settings where ventilation exchange may be inadequate. Overall, none of the case studies analysed mentions the implementation of specific safety devices in the 3D printing production environment.
Discussion
As highlighted in Paragraph 1, the sustainability of the construction sector is a growing concern for international policies and both public and private stakeholders. Investments in research and technological innovation are pivotal to supporting the green and digital transition, which encompasses environmental, economic, and social dimensions. Technological advancements within the business and industrial sectors play a crucial role in this transformation, aligning with broader regulatory efforts to promote sustainability.
Design choices made throughout the various stages of the additive manufacturing process are instrumental in determining both the sustainability of the process and the final building product, significantly influencing the overall sustainability of buildings.
Therefore, designers and stakeholders must be equipped with practical decision-support tools from the outset to fully understand the implications of their design and manufacturing strategies.
The overall framework presents a comprehensive survey of state-of-the-art research on AM products and process sustainability assessment related to the research developed in the state-of-the-art research REVERSING and R3NEW.
The results’ analysis highlights the potential of additive manufacturing processes to produce prefabricated sub-components for building envelopes that meet multiple sustainability parameters. The development of multi-axis robotic machinery has driven the integration of 3D printing into the industrial context, demonstrating significant progress compared to traditional prefabrication methods. This technology enables the production of small finishing elements (e.g., tiles) and larger components. Combined with computational design methods, it allows precise control over the entire manufacturing process, offering advantages across multiple dimensions.
Firstly, shape control facilitates advanced product customisation and enhances technology from both performance and technical perspectives (e.g., assembly and installation). The file-to-factory approach also allows for effective manufacturing process management to maximise the 3D printing phase performances (e.g., material printability and reduced printing times). Moreover, process control can be ensured through specialised software capable of monitoring machinery energy efficiency and the quality of production flows, thereby enabling continuous improvement of operational performance.
All the case studies reveal that small-scale 3D printing is a viable solution for producing high-quality prefabricated elements, with significant potential for controlling product and process sustainability. However, a review of the current literature highlights the need to develop further specific sustainability parameters that, although researched, still need to be systematically applied or certified within additive manufacturing processes. These parameters should be evaluated holistically to ensure comprehensive sustainability certification of both the process and the product, considering environmental performance and the impact on the health of users and workers during implementation and operation.
Below are four key points that have emerged as central to assessing and implementing the sustainability of building envelope sub-components and developing future research:
Materials and Applications
In Paragraph 2, the 13 chosen case studies were categorised by material type, with four falling under the “Bio-based Innovative Modules” category (CS.10, CS.11, CS.12, and CS.13).
Furthermore, Figure 5 highlights significant material differences influencing selection:
1.Organic Nature: Using organic or bio-based materials for innovative envelope subcomponents enhances the potential for the building envelope to function as a second skin, naturally interacting with its environment. However, even bio-inspired systems like CS.03, with auxetic silicone membranes, connect with the environment via sensors and mechanical systems, offering a more artificial interaction.
2.Material Circularity: Bio-based and natural materials perform well in circularity, allowing reintroduction into new production cycles. Similarly, certain plastics are recyclable, further promoting material reusability after their lifecycle.
The detailed analysis in Paragraph 3 shows that, in the domain of sustainable product innovation, the pivotal considerations encompass the incorporation of circularity into the product design and its interaction with its context and surrounding biological ecosystems. A meticulous approach to material selection, resource provenance, reuse potential, and recycling is crucial to ensure the efficacy of such innovations.
Product circularity
As Paragraph 3 observes, strategically managing product circularity to ensure the sustainability of envelope sub-components is highly complex due to various interrelated factors that often conflict.
Firstly, analysis of the datasheets reveals that AM processes were utilised to produce tailored sub- components specific to a building’s shape, structure, and environment. Additionally, 3D printing enables tile customisation (e.g., section and surface design) to achieve uniqueness and aesthetic impact, resulting in complex organic patterns (e.g. CS.01, CS.02, CS.04, CS.06, CS.07, CS.10). However, this level of customisation complicates product reuse and redesign. Therefore, recyclability and high maintainability are essential for evaluating product circularity.
Key evaluation factors include:
1.Material recyclability and re-printability without quality loss;
2.Durability, particularly for outdoor applications:
a.Material longevity;
b.Post-process finishes enhance durability.
1.dry-assembly systems enabling disassembly and replacement;
2.Transportability, modularity, dimensions, and weight.
Natural materials without post-processing (e.g., firing) reach the recyclability target but are less durable as in CS.11 and CS.12. Therefore, they are more suitable for indoor, controlled environments unless temporary use and degradation are planned (CS.10). On the contrary, ceramic products (CS.01, CS.02) present high durability, extending the life span of the exterior tile, but reducing the recycling potentialities.
Plastic components seem to show the most substantial circularity potential; however, plastic material subjected to recycling cycles undergoes progressive downgrading, preventing reuse for the same application unless combined with other materials (e.g., binders) [120]. Furthermore, data on LCA, finishing processes and energy consumption must be more comprehensive to analyse plastic products’ sustainability and ensure building envelope safety (e.g., fire resistance, UV protection, and emission toxicity) [51]. Further research on these aspects is crucial for improving the safe application of such components.
Energy consumption and Reduction of emissions
Phase 2 of the assessment and comparison of the datasheets, referring to the 13 selected case studies through the 24 Sustainability Parameters, revealed in Figure 5 a general absence of data concerning the Sustainability Goals ‘Energy Consumption’ and ‘Reduction of emissions’.
This gap highlights two critical areas for future research developments:
1.Energy consumption: The results reported in Section 3 demonstrate the necessity of incorporating measures to assess and regulate energy consumption and CO2 emissions throughout the industrial process. In addition, as indicated by May & Psarommantis (2023), merely measuring these parameters is inadequate; there is a necessity for the systematic implementation of standards in the measurement and reporting of energy consumption in AM processes. In addition, further research is required to systematically study the complex interactions during AM processes to understand its dynamics better and identify new ways to achieve energy efficiency.
2.Reduction of emissions: As pointed out in paragraph 3, the analysis of the case studies has shown a general lack of information, not only on the more immediate aspects directly related to consumption and, therefore, to the carbon footprint of the manufacturing process (e.g. energy consumption, the environmental impact of robots) but also an absence of information related to the origin of the materials used (e.g. are they local materials? do they come from sustainably managed sources?).
This information gap, perhaps even in terms of communication, emphasises the need to introduce a system supporting the sustainability certification of innovative materials used in 3D printing processes and the elaboration of LCA analyses of industrial products made through AM processes. This would increase awareness and the public dissemination of innovative processes that achieve a real sustainability target.
Workers’ safety and health
The analysis of the synthesis matrix of the Phase 2 Assessment and Comparison of the 13 case studies according to the 24 selected Sustainability Parameters revealed a general lack of data referring to SP.24 ‘Workers are not exposed to the emission of volatile organic compounds (VOCs) and ultrafine particles (UFPs) during the printing process’ referring to the Sustainability Goal ‘Work safety and health’.
A review of the literature has shown how the most recent research, especially following the boom in the use of plastic materials for both small-scale prototyping and industrial-scale 3D printing, has focused on analysing the impact of FDM and SLS printers on air quality in the working environment.
Research shows that various factors affect air quality with particular reference to 1) emissions of volatile organic compounds (VOCs) and 2) ultrafine particulate matter (UFPs).
The main factors are as follows:
a. printing temperature and extruder diameter;
b. type of material used;
c. the working environment (e.g., the presence of controlled mechanical ventilation at the machinery);
d. printer maintenance operations (e.g. cleaning)
This research highlights the critical need for regulatory frameworks to safeguard workplace health, citing the case studies conducted using the plastic materials CS.03, CS.04, CS.05, CS.06, CS.07, and CS.09. In alignment with recent studies on the subject and addressing the data gaps identified during the analysis phase, the study advocates for the development of regulations and guidelines aimed at mitigating risks associated with toxic emissions, thereby ensuring safe working environments. Furthermore, additional research must be conducted focusing on all stages of the manufacturing process, including post-processing operations or procedures following the printing phase. Such studies should also encompass a broader range of materials (e.g., composites, bio-based materials) and printing families to provide a more comprehensive analysis.
Conclusions
The research conducted within the REVERSING and R3NEW projects has defined a decision-support tool designed for researchers, designers, and industry professionals developing AM processes and 3D-printed building envelope sub-components. The presented results have contributed to creating a system for mapping sustainable building envelope products to support stakeholders in the construction sector in assessing the impact of design and production choices on the final sustainability of the 3D-printed building process and product.
Through a state-of-the-art analysis, this research investigates effective strategies to improve the sustainability of the manufacturing process and product, considering specific design, printing, and post- production requirements. Finally, it identifies directions for future research to improve critical aspects identified during the study.
A significant limitation of this research has been the lack of data in several crucial areas, including but not limited to energy efficiency, the environmental impact of the manufacturing process and product from cradle to grave, and air quality during the printing and post-production stages. To address this limitation, a dedicated section (Paragraph 2.3) was included to discuss the accessibility and quality of the data available in the literature, foster transparent dissemination within the scientific community, and advance research in these and other related fields.
In the initial phase of this study, a qualitative research approach was employed to establish a scientific framework for advancing AM technology in the construction sector, taking into account the inherent complexity of the variables involved. Building on the findings of the initial research phase, the next stage of the project concerns the evaluation and comparison of sustainability parameters. Implementing this stage requires defining quantitative assessment parameters based on existing literature and their application to case studies. The case studies focus on innovative envelope sub-components produced through Additive Manufacturing processes. The aim is to contribute to the existing body of research on the quantitative evaluation of the sustainability of the Additive Manufacturing process and its industrial building products.
Future research in AM for construction should address the critical aspects highlighted in this study, many of which remain under active investigation. As AM technology continues to disrupt the construction industry, further exploration is needed in key areas such as 1) improving energy efficiency in the manufacturing process, 2) assessing the environmental impact of the entire life cycle of the manufacturing process and product, and 3) ensuring safe air quality during the printing and maintenance phases. Addressing these challenges will be essential for advancing the sustainability of AM in construction and supporting the broader adoption of this technology in the building sector.